Sheet Metal Design – Advantages & Associated Challenges
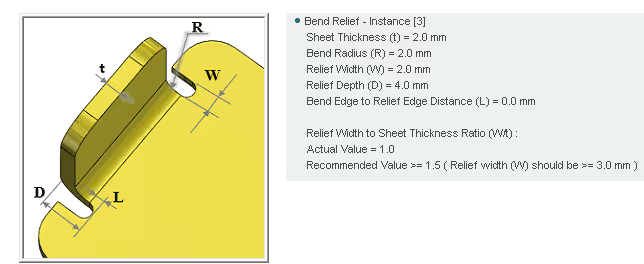
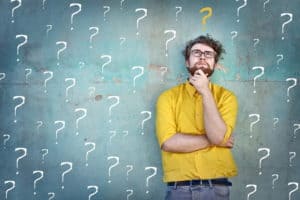
Sheet metal design holds a very important place in manufacturing industries that you may have noticed that from home appliances to industrial machines, most of them are enclosed in sheet metal.
Have you thought about why?
Applications of sheet metal are not limited to enclosures they have numerous other high-end applications such as making the aerodynamic profiles of vehicles and planes.
Sheet metal is also used in structural applications such as making frames and roofs. Containers are also one of the numerous applications of sheet metal. HVAC systems are also one of the major applications of sheet metal, ducts made of sheet metal are used to supply air into the target space.
Sheet Metal for Making Enclosures
These are just some of the reasons that designers choose to use sheet metal for making enclosures.
- Manufacturing with sheet metal is reasonably cheaper and easier, it is mostly associated with forming processes.
- Manufacturing can be carried out on a small scale, there isn’t any requirement of high-end machining centers. For forming a product out of sheet metal mostly a hydraulic press is employed with different tools to perform a variety of operations.
- CNC plasma cutting technology has added to the applications of sheet metal due to its high precision and automated cutting of any shape.
- Sheet metal working saves time due to simpler processes for example in case of solid you need to drill a hole but for sheet metal, you have to punch a hole. For making a slot in a solid, milling is required but in case of sheet metal, CNC plasma cutting, or a simple punch can do the job.
- The weight of a sheet metal designed product is significantly less, that is why mostly enclosures are made of sheet metal and mostly aluminum sheets are used, due to a higher strength to weight ratio.
After having discussed the advantages of sheet metal manufacturing you might think about the challenges associated with sheet metal design? Sheet metal design requires special consideration because due to the smaller thickness of the sheet, the area to resist shearing is very small which makes the holes in sheet metal very vulnerable to shearing. So, the holes are always designed at a safe distance from the edge of the sheet. Sheet metal designing is mostly associated with bending and forming. When a bend is to be formed near the edge, provision for bend relief is made so that material may not tear near the bend.
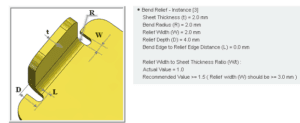
Figure 1 Bend Relief
https://dfmpro.geometricglobal.com/files/2018/07/Benefits-of-Bend-relief.png
Figure 1 Bend Relief
https://dfmpro.geometricglobal.com/files/2018/07/Benefits-of-Bend-relief.png
The extent to which a sheet can bend is material dependent, so sheet metal designing is material-specific because the bend radius is dependent on both material and sheet thickness. As the spring back effect is material dependent the bend angle is also material dependent it may be greater or less than the desired angle if you change the sheet material. How to overcome this limitation of material specific design?
To account for the difficulty of variation of parameters from the design while manufacturing, k-factor is employed in sheet metal design, to determine the bend allowance and bend deductions because it is based on the position of a neutral axis on the bend profile, which estimates the amount of stretching and compression occurring due to the bend it may be noticed that neutral axis is shifted towards the inner radius of the bend as the bend radius is decreased.
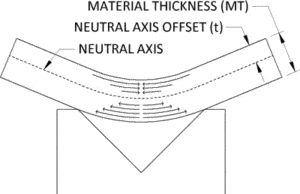
Figure 2 Parameters affecting k-factor.
http://sheetmetal.me/formulas-and-functions/k-factor/

K-factor is employed in most CAD software to account for allowance of material and thickness of the sheet. Due to the abundant use of sheet metal in manufacturing industries almost all the reputed CAD software packages have a separate module to model for sheet metal design. In sheet metal module, there are different options for modelling such as to fold or unfold a sheet, bending, creating a base flange, swept flange, edge flange, different types of hems, using the forming tool etc. Modeling in sheet metal module uses an entirely different approach for example if you create a base flange of a sketch containing two perpendicular lines and a sharp corner at joint, software will automatically specify the bend radius and no sharp corner will be seen. So, a parametric model employing k-factor can serve to generalize the sheet metal design. With the parametric model, you just have to change the k-factor for new material and leave the rest on software, it changes the associated design parameters.
After having read the applications and challenges associated with sheet metal design and modeling, let me introduce you to the professionals in providing designing services. CAD / CAM Services has a team of experienced professionals providing designing and modeling services in SolidWorks, CATIA, UG NX.
CAD / CAM Services possesses a vast experience in designing Aeroplane Parts, Pressure Vessels, Tanks and a variety of other products. They have the clients who are giants in their respective fields like Boeing, Thompson and Coca-Cola are a few of the lot. For any work regarding 3D modeling, Designing, Reverse Engineering get a quote from CAD / CAM services by visiting https://www.cadcam.org/.
Recent Posts
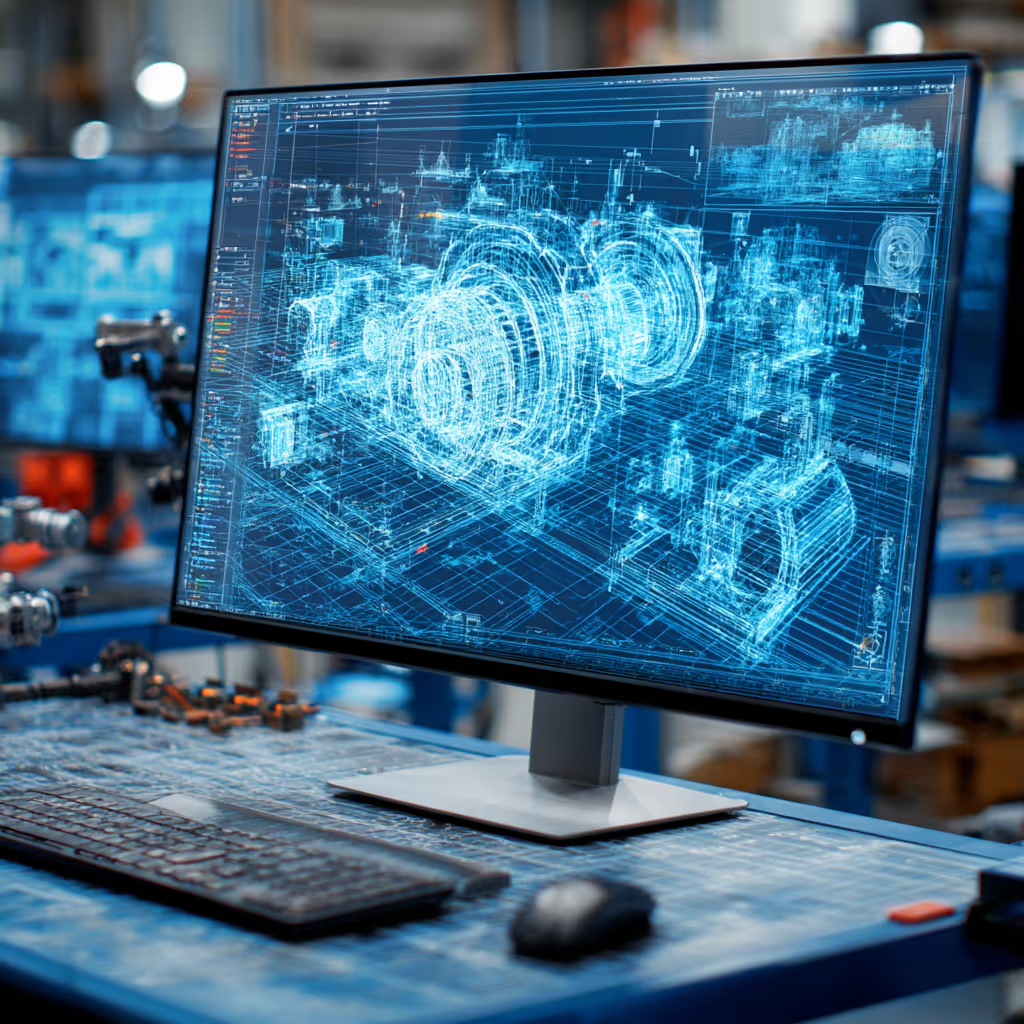
Tips for Picking the Perfect 3D CAD Viewer for Your Needs
This guide will teach you about 3D CAD viewers and outline considerations to make before picking the right one. We review 5 options and pick a clear winner.
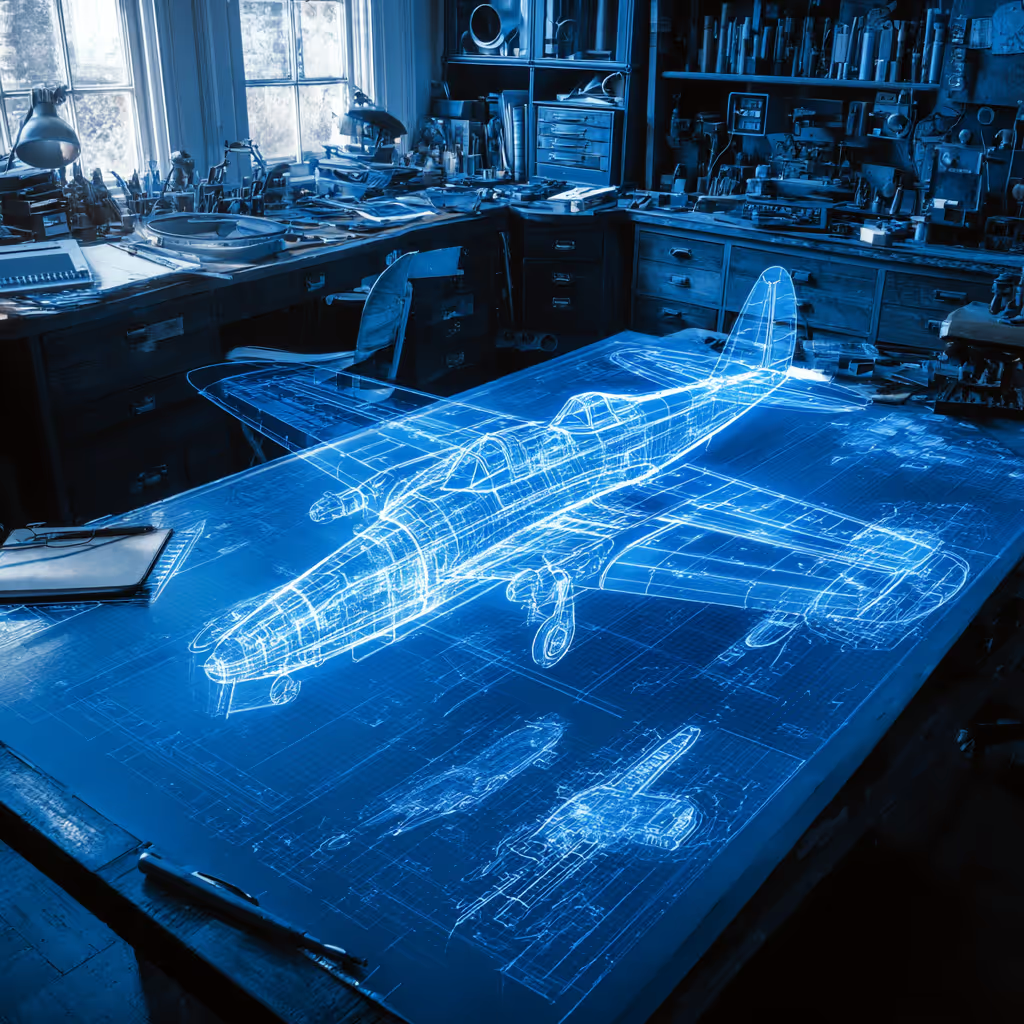
In this guide, you’ll learn how CAD/CAM Services can save you time and money during each digitization project. Digitization can make manufacturing faster than ever before.
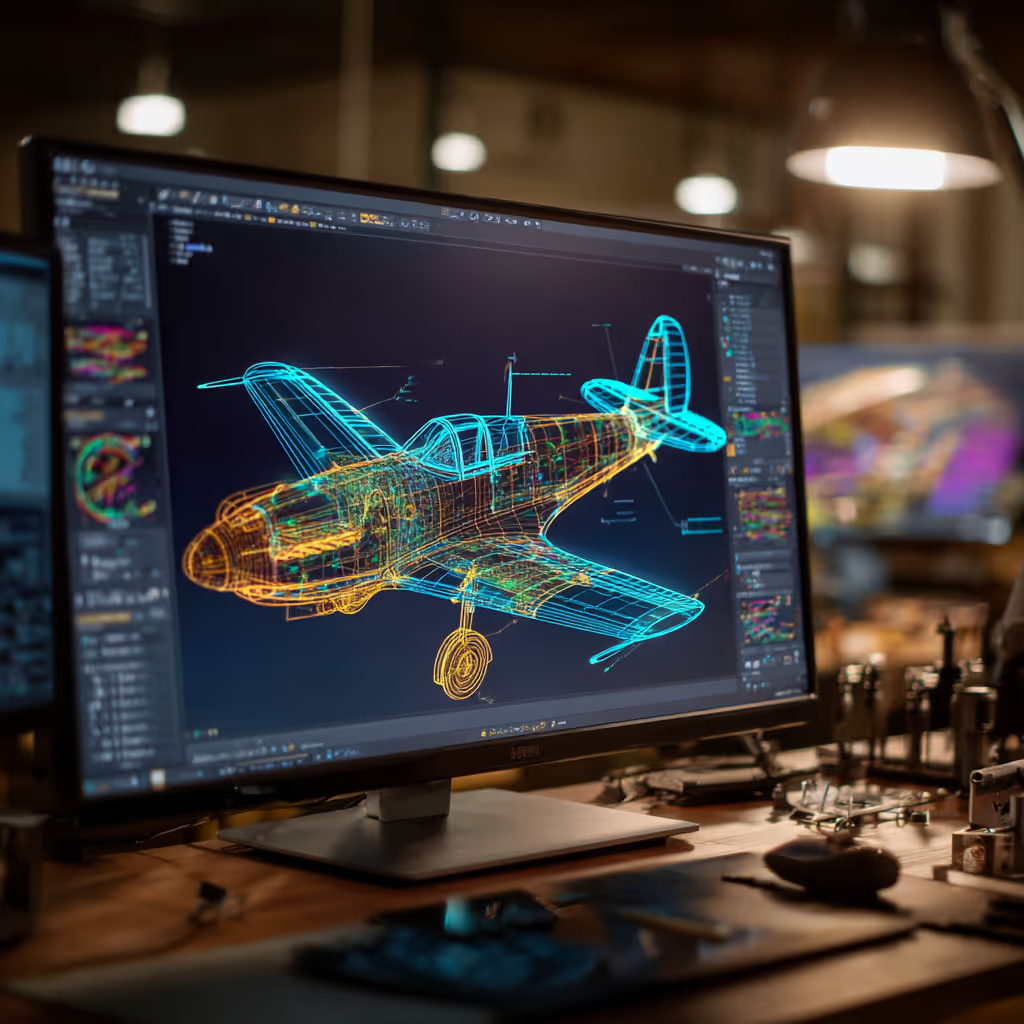
How to Build an Aircraft Model by Converting 3D-Scanned STL Files into Functional 3D STEP Files
This in-depth guide will teach engineers how to use 3D-scanned aircraft files and transform them into manufacturable 3D STEP files with fewer mistakes.