The Wonderful World of Sheet Metal Design
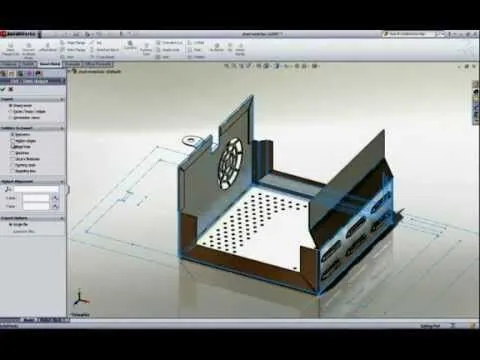
The Wonderful World of Sheet Metal Design
Sheet metal is used for many different design options and applications – from artistic sheet metal sculptures to automobile bodies, airplanes, and medical tables. In fact, a world without sheet metal would be very different from the world we know. Designers, engineers, and artists appreciate the material’s durability and flexibility.
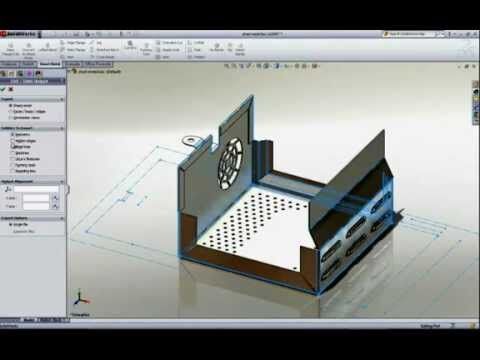
What is Sheet Metal and Why It’s Important
Sheet metal is made by an industrial process, using aluminum, brass, copper, steel, tin, nickel and/or titanium, that is formed into thin, flat pieces. It is one of the fundamental materials used in metalworking and it can be cut and bent into a variety of shapes. Thicknesses can vary significantly; extremely thin thicknesses are considered foil or leaf, and pieces thicker than 6 mm (0.25 in) are considered plate. The thickness is specified as a gauge, with a larger gauge number representing a thinner metal. Sheet metal is available in flat pieces or coiled strips.
Gauge, metal, and type used are dictated by the end user. Thinner gauges and softer metals are specified for decorative use, while heavier gauges and harder metals are used where strength is required. Some applications such as automobile bodies and aerospace require sheet metal that is both strong and lightweight. Additionally, sheet metal made from iron or other materials with high magnetic properties is used in transformers and electrical machines. Sheet metal was used historically for plate armor worn by the cavalry.
In 2011, the sheet metal industry was worth almost $20.5 billion in the United States. There were 4,000 firms employing 106,000 sheet metal workers.
Designing for Sheet Metal
Any design process begins with an idea which is transformed into a graphical description of a proposed device. Often this graphical description is nothing more than a rough sketch. The sketch is the first external representation of the idea, which then must be refined into details of the concept. CAD, and in particular, 3D CAD, is a tool that shortens this conceptual process by enabling the merge of the idea with qualitative and quantitative processes. By working within a 3D CAD program, the designer can modify the concept, gradually turning it into a more concrete solid character. At some point, as it becomes better defined, precise analytical tools can be applied to determine the validity of the design concept.
During this design process, the designer is concerned with a large set of variables, some continuous (like the weight of a part) some belonging to discrete “point sets” (like the material: type, strength, and gauge of the sheet metal). Moreover, these variables are interrelated or cross-coupled, in a very complex way. Some of the cross couplings are weak, some are strong. If the relationships happen to be linear, the cross couplings are constant in strength, but usually, the relationships are non-linear, and the mutual influences of the various variables change with their values.
By using 3D Solid Modeling software, such as SolidWorks, for the design process, the designer can “virtually” create nearly anything that his imagination can conceive. This 3D virtual design process enables him to detect and correct any design flaws that may have passed unnoticed in a 2D design process. This is especially critical in manufacturing applications, where design and fit problems on the shop floor cost both time and money.
Fabricating in Sheet Metal
3D CAD also enables more efficient sheet metal processing by enabling a fast and reliable workflow that moves quickly from the design process into fabrication. Typical sheet metal fabrication includes bending, folding and cutting sheet metal to make items like: brackets, cabinets, housings, washers, shelves, covers, doors, channels, pans, copper bus, levers, gussets, plates, panels, and much more.
Processes for fabrication include laser cutting, punching, bending, stamping, as well as additional secondary operations that add precision to the sheet metal fabrication of parts and assemblies.
Recent Posts
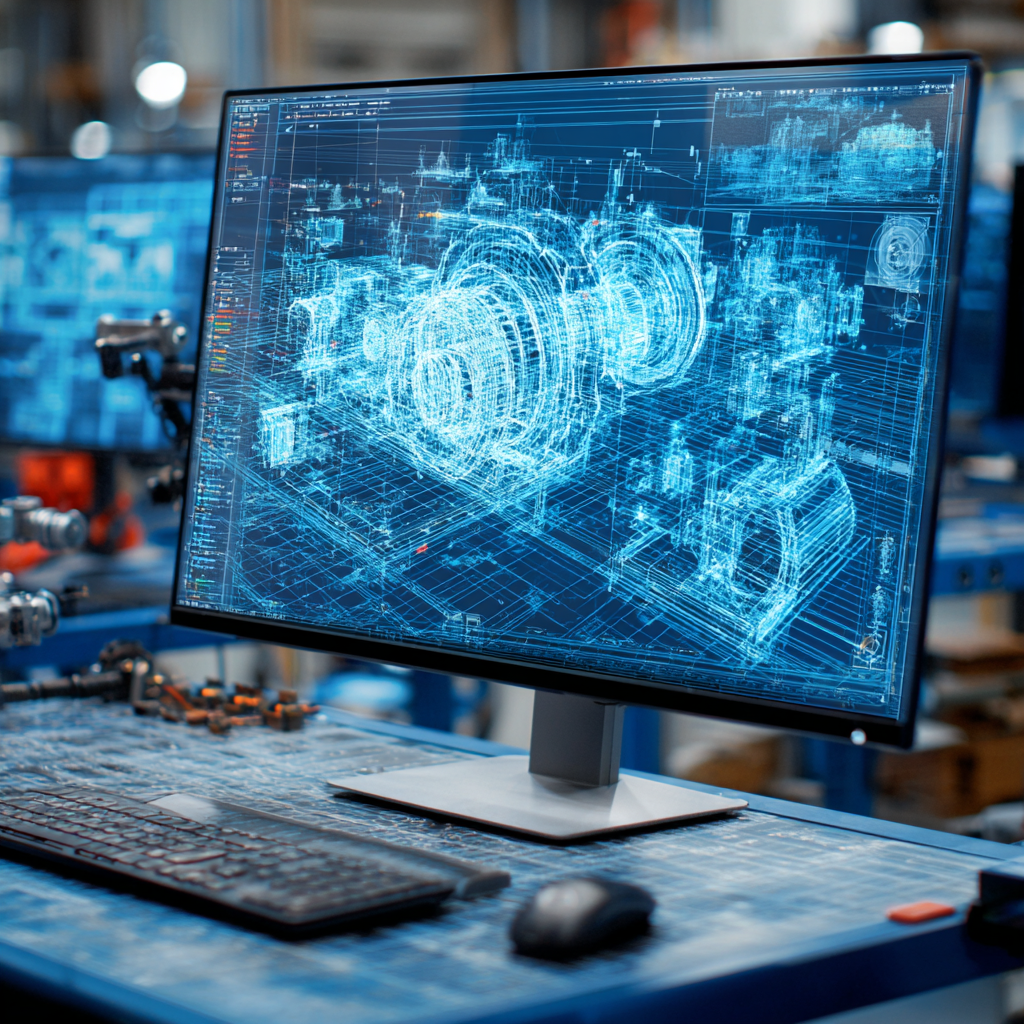
Tips for Picking the Perfect 3D CAD Viewer for Your Needs
This guide will teach you about 3D CAD viewers and outline considerations to make before picking the right one. We review 5 options and pick a clear winner.
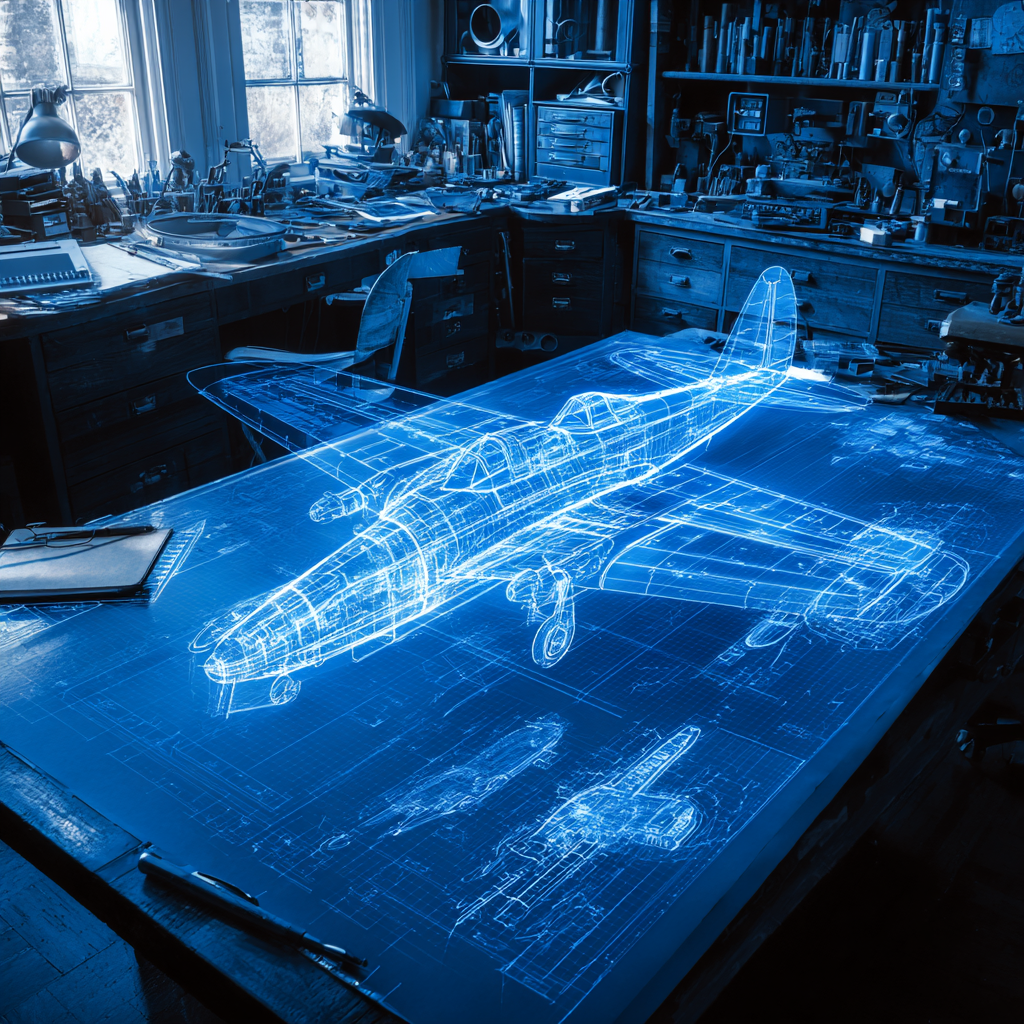
In this guide, you’ll learn how CAD/CAM Services can save you time and money during each digitization project. Digitization can make manufacturing faster than ever before.
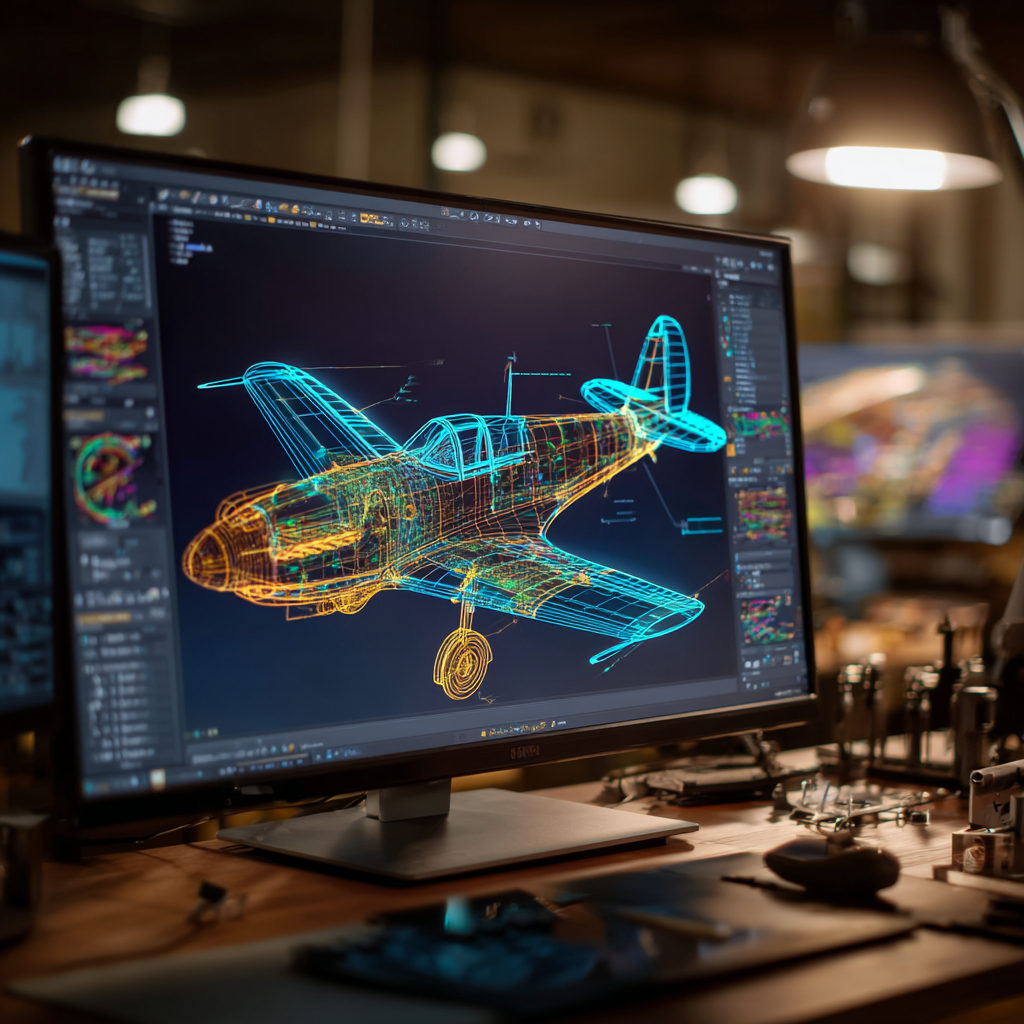
How to Build an Aircraft Model by Converting 3D-Scanned STL Files into Functional 3D STEP Files
This in-depth guide will teach engineers how to use 3D-scanned aircraft files and transform them into manufacturable 3D STEP files with fewer mistakes.