How CAD / CAM Services Use CATIA Tool Test Models
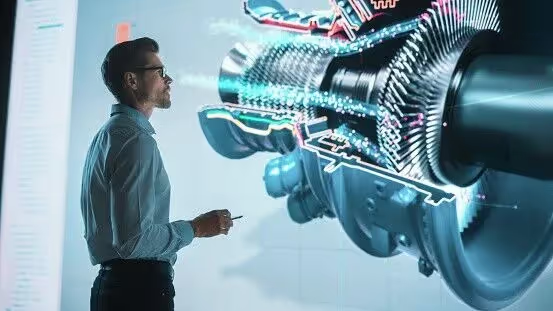
Quality assurance is a critical aspect of any manufacturing process. It’s particularly crucial when it comes to tool models. Advanced software tools like CATIA provide powerful capabilities for testing tool models, ensuring they meet the required standards and function as intended.
In this guide, we will explore the benefits of using CATIA for tool model testing, how you can leverage it, and how outsourcing these essential tasks to CAD/CAM Services can save you time and money.
What Is CATIA?
CATIA is a robust CAD/CAM software solution developed by Dassault Systèmes. CATIA is really popular because of its powerful capabilities in 3D design, engineering, and manufacturing. Its comprehensive suite of tools makes it an excellent resource for a broad range of applications, including tool model testing.
Understanding Tool Models and Testing
Tool models represent the physical tools used in manufacturing processes. They are essential for understanding how a tool will look, act, and perform under real-world conditions.
Tool testing is the process of verifying the functionality, durability, and safety of a tool before it is manufactured, by using the model. The purpose is to identify any potential problems and fix them before production — which is a quick way to save time and money.
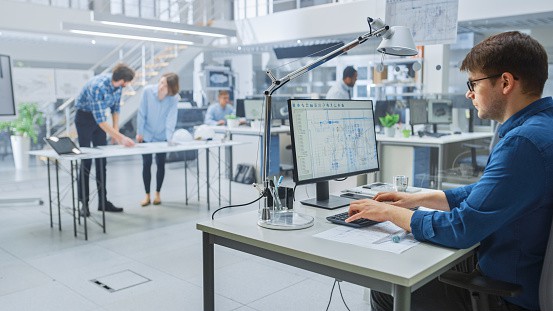
Why Should You Test Your Tool Models Before Production?
Tool model testing is a critical step in the product development process. It helps prevent costly mistakes and redesigns, making sure that the tool will function correctly.
Testing your tool will make your prototype or production process much faster and less expensive. If you find a problem after making the part, it’s too late. Catching the same problem in the modeling phase is the perfect time to fix it before manufacturing starts.
Benefits of Using CATIA to Test Your Tool Models
CATIA provides a range of features for effective tool model testing, including:
Simulation
CATIA’s powerful simulation tools allow you to mimic real-world operating conditions, providing invaluable insight into your tool’s performance. You can adjust parameters such as load conditions or environmental factors, which can test the tool’s durability and reliability under a range of circumstances.
Fitment Check
Ensuring the correct fit and assembly is crucial for any tool’s performance. With CATIA, you can simulate the assembly process and the interaction between different components.
This is where you can check dimensional clearances and tolerances. A fitment check will show you if parts will interfere when you try to assemble them in real life.
Material Check
Material selection plays a vital role in a tool’s performance. With CATIA, you can simulate the impact of different materials on your tool’s behavior, helping you choose the most suitable material for your specific application. You can test attributes like durability, weight, and resistance to heat or corrosion.
You can use the material properties of 6061 aluminum, then do an FEA of the part. The result will act exactly like aluminum does, thanks to the material properties within CATIA.
Finite Element Analysis (FEA)
Speaking of FEA, CATIA’s FEA functionality lets you run detailed stress and strain tests, offering insights into potential points of failure in your tool design. By identifying these areas, you can refine your design to enhance the tool’s reliability and lifespan.
If your part fails the FEA, you have a chance to strengthen the design before manufacturing starts.
Increased Confidence
When you combine all of the functionality in CATIA, you’re left with a tool that you can trust. You’ll have more confidence with every design, since you already went through all of these checks.
Cost Savings
The bottom line is that CATIA can save your company a lot of money. Between finding dimensional issues earlier and minimizing the size of your part, your team can save a lot of money on every design.
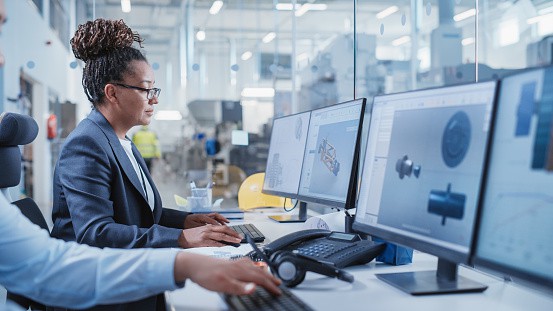
How to Use CATIA to Test Your Tool Models
When our team performs tool model testing in CATIA, we follow a few steps. Here is what a typical project breakdown looks like:
Model Creation
Begin by creating a 3D model of your tool using CATIA’s robust design tools. Make sure to include all relevant details, such as material properties and component interfaces. Make sure the part is in 3D and has the correct dimensions.
Simulation Setup
Set up the simulation based on the conditions you want to test.
For an FEA simulation, you would need to apply the loads, set the constraints, and specify how precise you need the results to be.
Test Execution
Run the simulation and observe how your tool model performs. Look for any signs of stress, deformation, or failure that might indicate a potential issue.
Analysis
After running the simulation, analyze the results. CATIA provides a variety of tools for this purpose, including visualizations, charts, and reports. Look for areas where your tool model performed well and areas where improvements might be necessary.
Compare the stress results to the mechanical properties of the material you’re using, like the ultimate yield strength (which tells you when the part will break). Ensure there is a margin for error, called a “factor of safety”. If the results are 1/3 of the ultimate yield strength of your material, then you have a 3.0 factor of safety.
A good factor of safety ensures the part won’t break when it’s used in real life.
Iteration
Based on the results of your analysis, make any necessary adjustments to your tool model. Then, run the simulation again to see how these changes impact performance. Repeat this process until you are satisfied with the tool’s performance.
The Advantage of Outsourcing Your Tool Model Testing
Outsourcing your tool model testing to an experienced team like CAD/CAM Services can offer several advantages. Our expert engineers have in-depth knowledge of CATIA and can conduct thorough tool model tests, ensuring optimal results.
In addition, outsourcing these tasks frees up your team’s time to focus on other critical aspects of your operation, providing a more efficient use of resources.
CAD/CAM Services has been helping businesses optimize their manufacturing processes for over 30 years. Regardless of what industry you’re in, our CATIA tool model testing solutions can help you achieve your goals.
Conclusion
Tool model testing is a crucial aspect of the manufacturing process. By leveraging the powerful capabilities of CATIA, businesses can enhance their testing procedures, save time and money, and improve the quality of their products. Trust CAD/CAM Services to provide top-notch CATIA tool model testing services for your business. Let us help you optimize your manufacturing process, get a free quote today.
Recent Posts
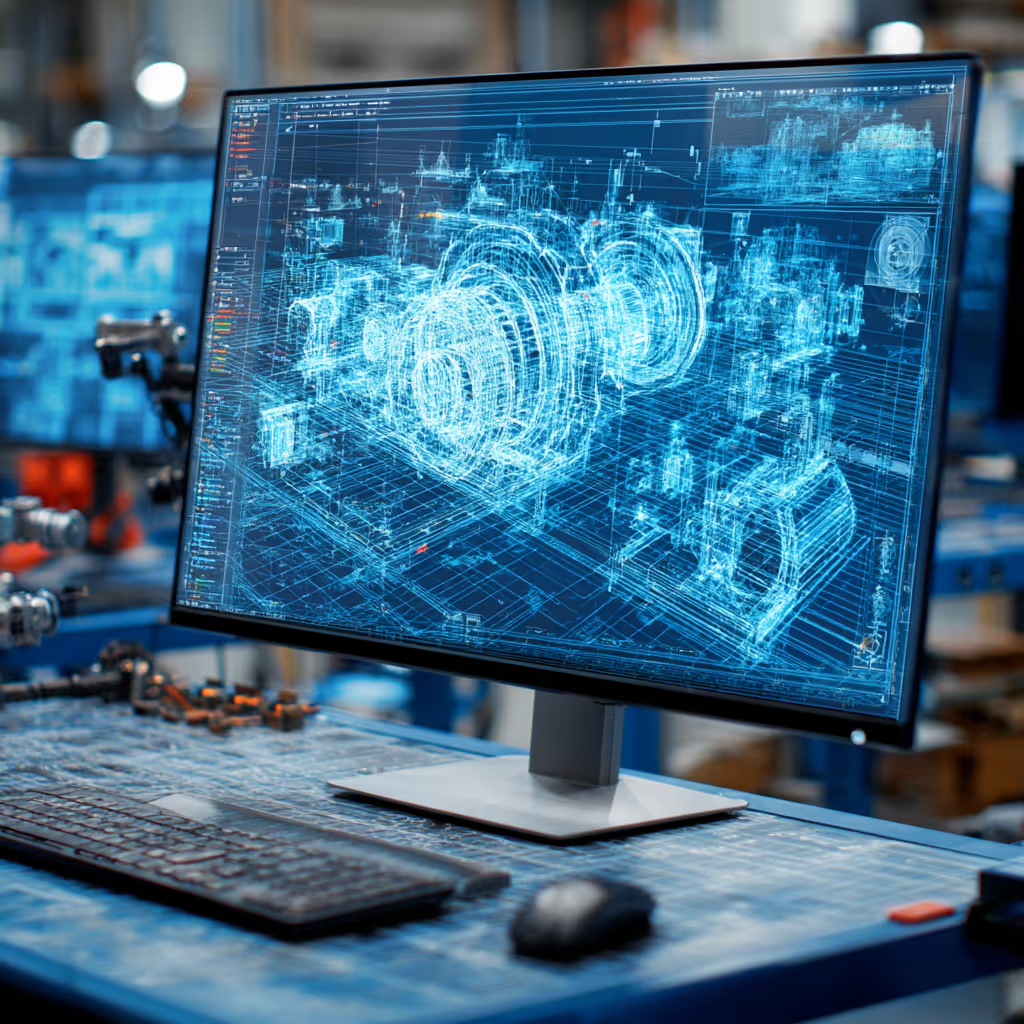
Tips for Picking the Perfect 3D CAD Viewer for Your Needs
This guide will teach you about 3D CAD viewers and outline considerations to make before picking the right one. We review 5 options and pick a clear winner.
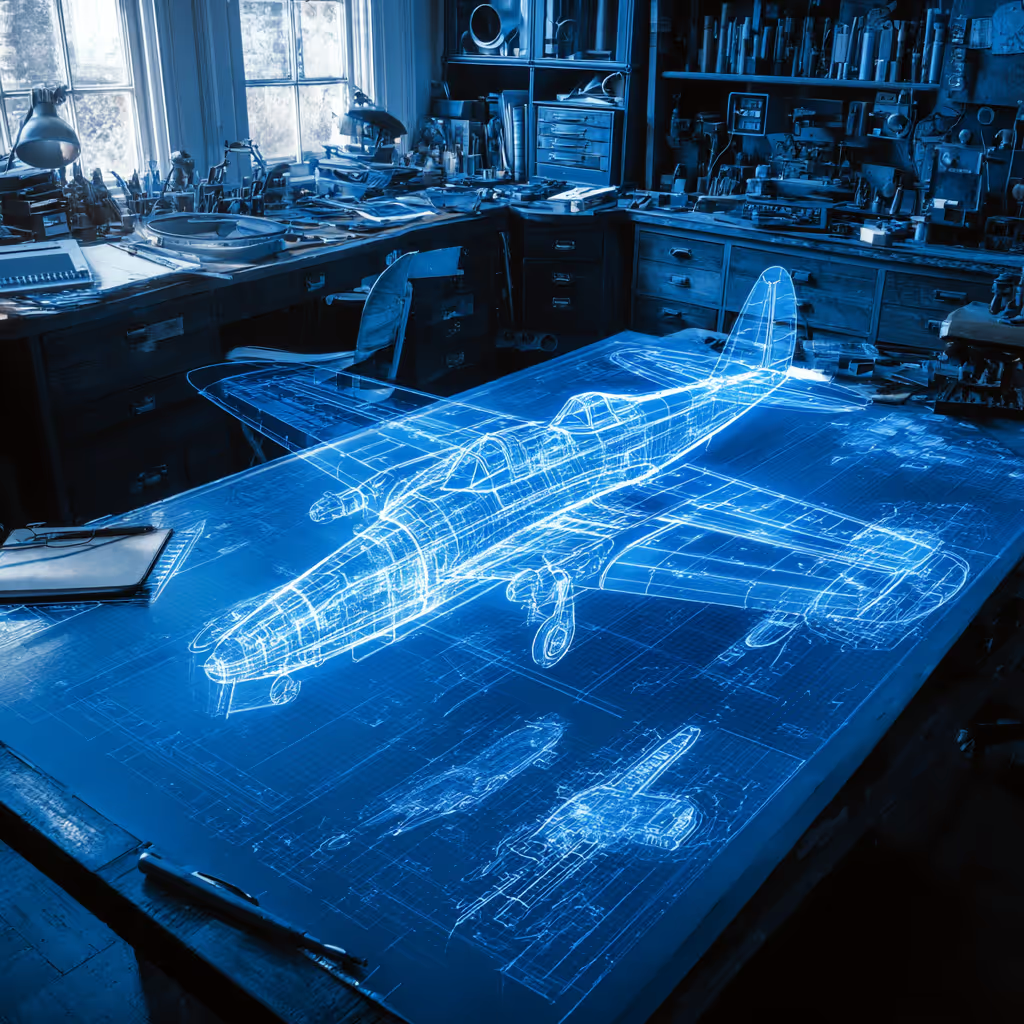
In this guide, you’ll learn how CAD/CAM Services can save you time and money during each digitization project. Digitization can make manufacturing faster than ever before.
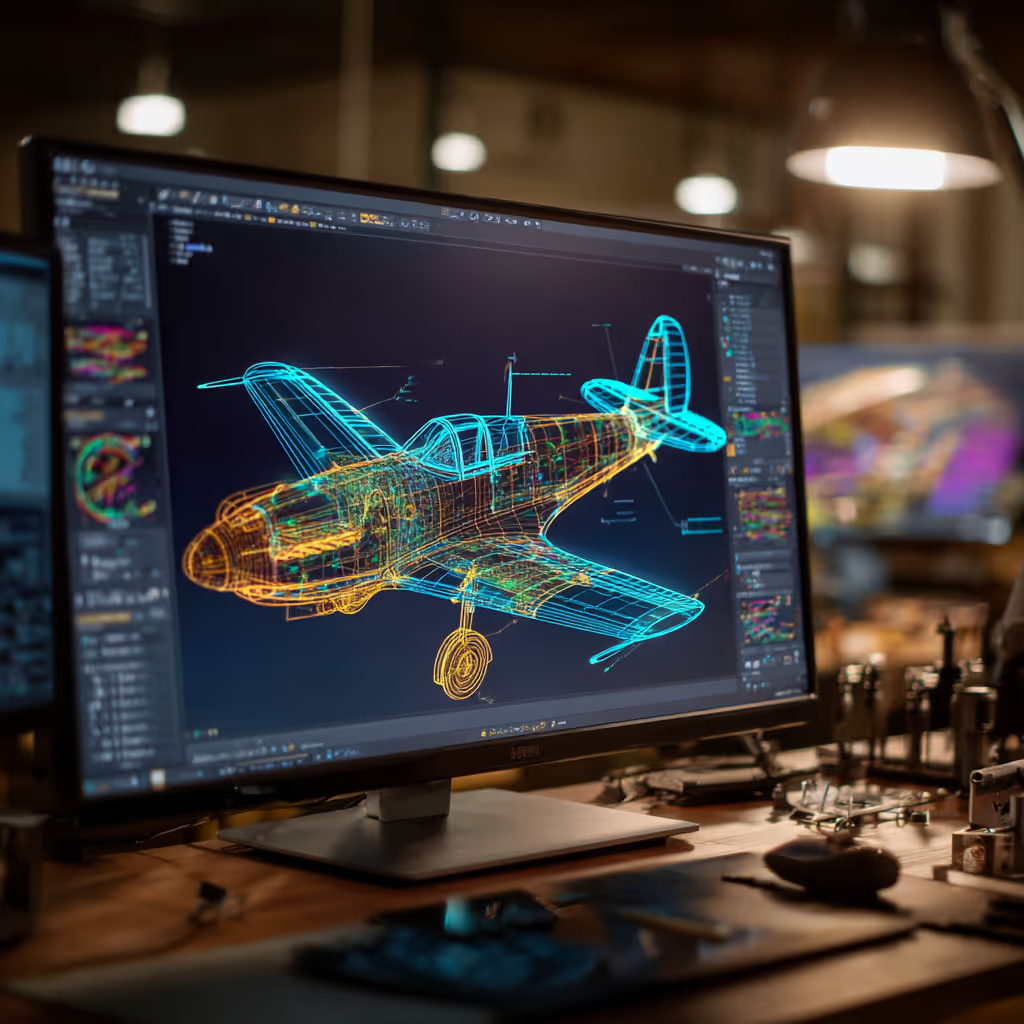
How to Build an Aircraft Model by Converting 3D-Scanned STL Files into Functional 3D STEP Files
This in-depth guide will teach engineers how to use 3D-scanned aircraft files and transform them into manufacturable 3D STEP files with fewer mistakes.