Why Companies Convert 2D CAD Designs to 3D
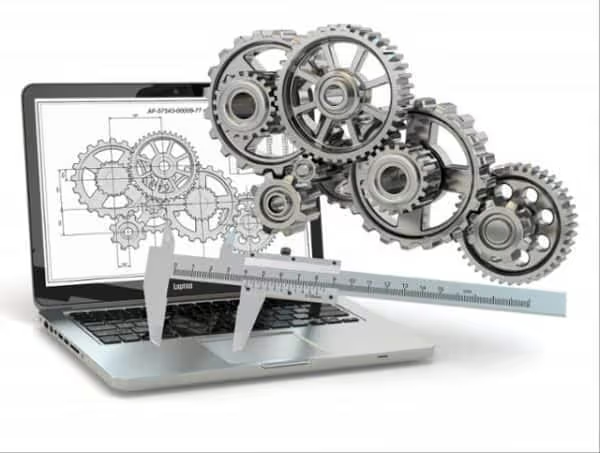
Why Companies Convert 2D CAD Designs to 3D
The early versions of CAD were all 2D CAD, but in today’s design world, 3D models are the preferred option for easy visualization.
Just as the 2D CAD, first introduced in the 1980s, quickly become popular, 3D CAD has become the preferred method of visualizing a CAD design. So, what do you do with all of your legacy 2D CAD drawings now that you’re doing so much in a 3D design system, such as Revit, Solid Works, CATIA, or another 3D program? And how do you incorporate 2D design, since 2D drafting is still widely in use?
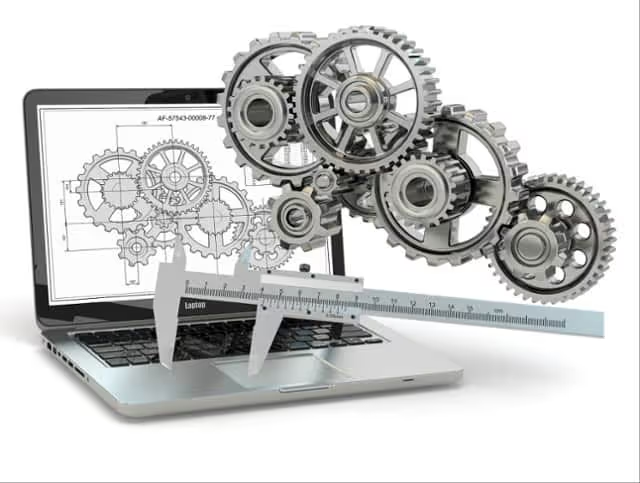
It’s important to be able to convert both legacy drawings and newly created 2D drawings into 3D models. This conversion from 2D to 3D is important in aiding the visualization of the finished product. Our brains are simply better able to do this type of visualization from a 3D virtual object than they are from a 2D drawing.
While 2D drafting tools provide sufficient data about an object, only 3D modeling techniques can help engineers and designers to spot problems and make solutions for these problems before the actual building of the physical object. So, 3D technology can provide companies with competitive advantages
In fact, despite the importance of 3D, some CAD designers may still focus on the traditional 2D drafting systems (vector drafting), while others may use 3D design systems which deal in solid and surface models. Some modern CAD packages even allow rotations in three dimensions, allowing viewing of a designed object from any angle. Most modern CAD software is capable of dynamic mathematical modeling, in which case it may be marketed as CADD, which stands for computer-aided design and drafting.
Taking a Drawing from 2D to 3D
The process of converting a 2D drawing into a 3D model can seem complicated, even when using some of the popular 3D modeling tools like AutoCAD, SolidEdge, and Microstation. Two of the most important parts of the conversion process are (1) understanding the process itself; and, being well-schooled in the software that you’re using. Remember that the aim of this technology is to simplify the process of creating 3D part models from existing 2D CAD drawings.
It’s also important to realize that different types of CAD require the CAD operator to think differently about how to use them to design.
2D systems provide an approach to the drawing process that is similar to the old-school hand drafting but without concern over scale and placement on the drawing sheet that accompanied hand drafting. Computerized drafting enables scale and placement to be adjusted as required during the creation of the final draft.
3D systems require the CAD operator to use what is referred to as “design intent”. Design intent refers to the process of capturing intelligence in the 3D model by means of parametric and geometric relationships that define the fit and function of the part.
The “perfect world” representation that is created when design intent is part of the formula enables future revisions and changes of one section within the model to be interpreted throughout the design so that the engineer can see the results of the change in the overall design, rather than just as a basic shape change in one section. This means that the designer must consider the consequences of any changes that he makes.
This also goes a long way toward explaining why companies convert 2D designs to 3D CAD.
Recent Posts
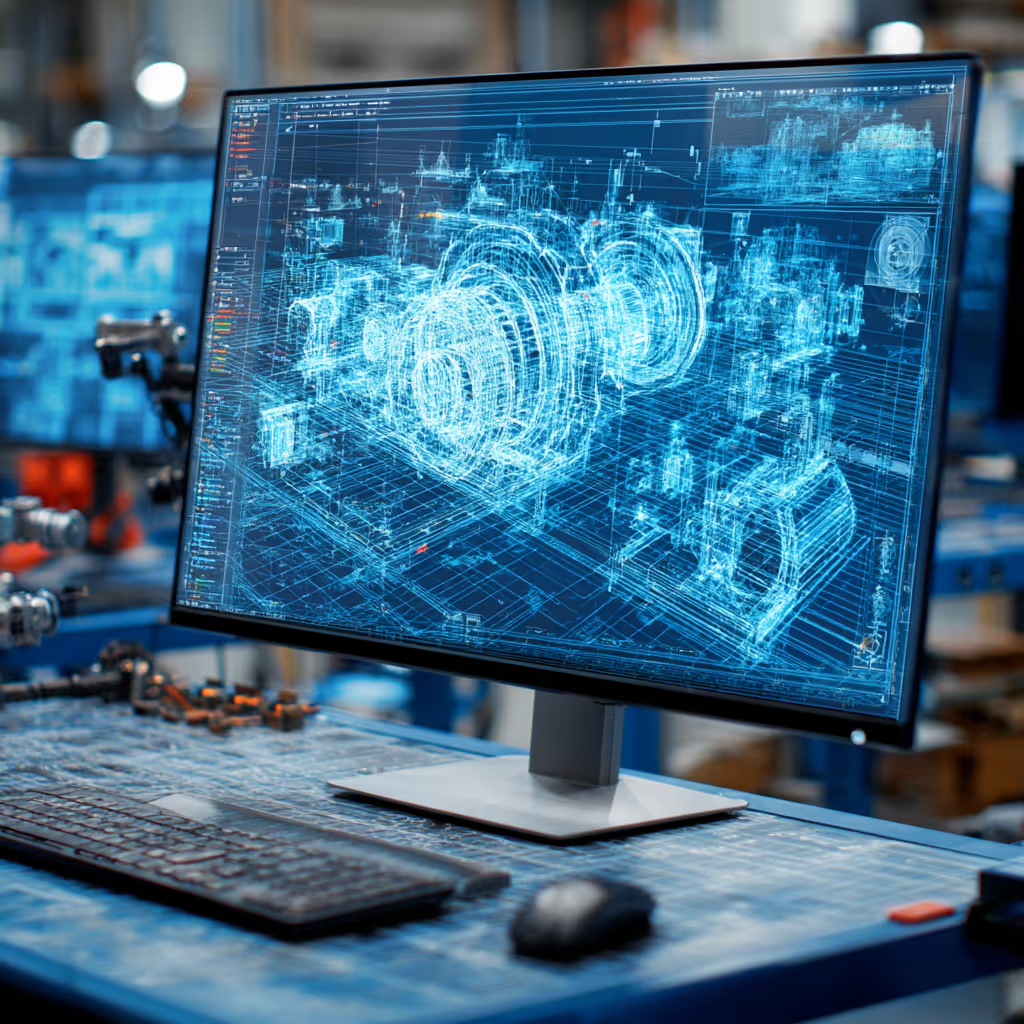
Tips for Picking the Perfect 3D CAD Viewer for Your Needs
This guide will teach you about 3D CAD viewers and outline considerations to make before picking the right one. We review 5 options and pick a clear winner.
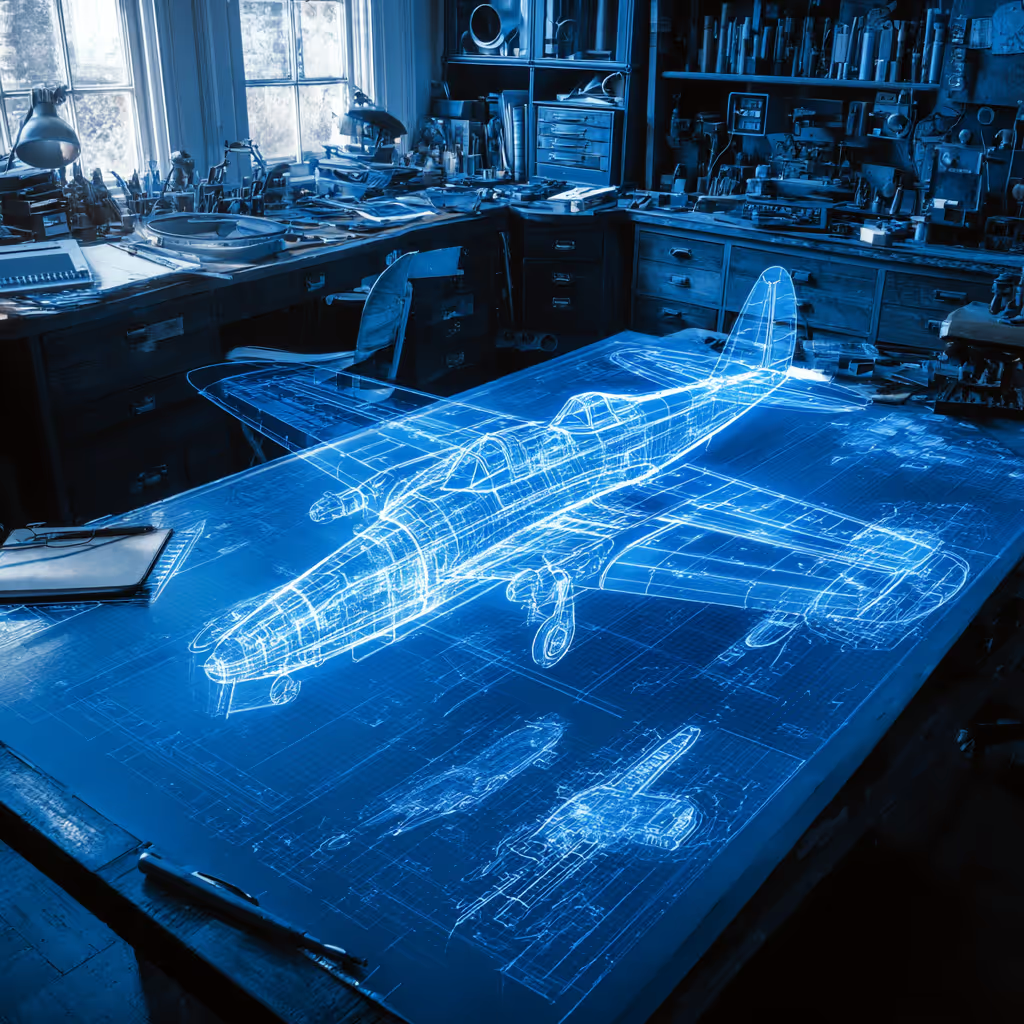
In this guide, you’ll learn how CAD/CAM Services can save you time and money during each digitization project. Digitization can make manufacturing faster than ever before.
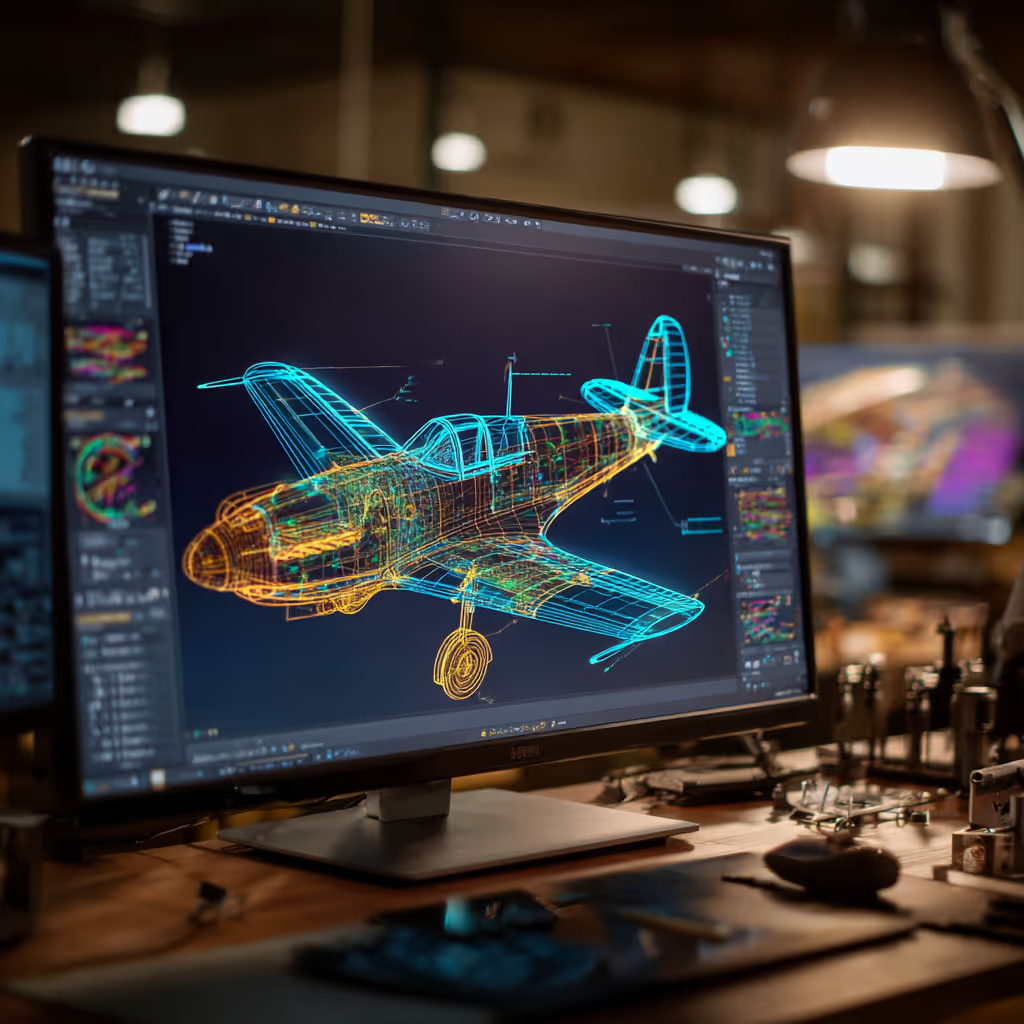
How to Build an Aircraft Model by Converting 3D-Scanned STL Files into Functional 3D STEP Files
This in-depth guide will teach engineers how to use 3D-scanned aircraft files and transform them into manufacturable 3D STEP files with fewer mistakes.