The Importance of 2D to 3D CAD Conversions
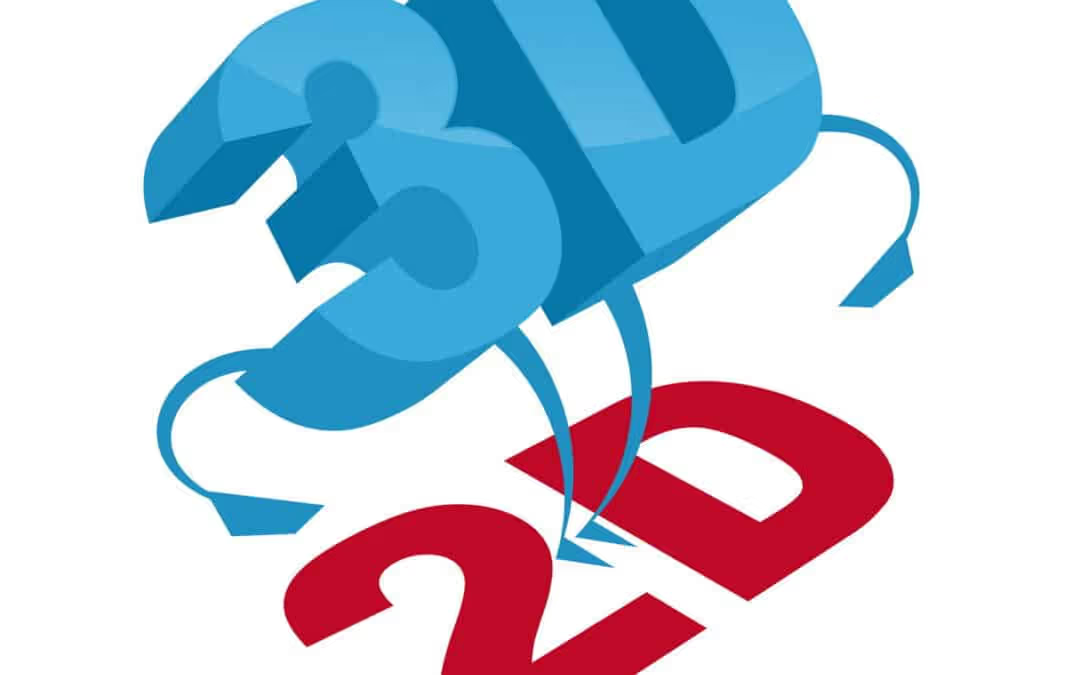
If you have a backroom full of 2D hand drawings, you could be losing a lot of efficiency in your company. Doing a simple conversion from 2D to 3D will make manufacturing easier, avoid a lot of human error, and triple-check the quality of your designs.
In this short guide, we’ll discuss the importance of 2D to 3D CAD conversions, and we’ll teach you how to do this conversion easily.
Importance of 2D to 3D CAD Conversions
We’ve done projects for companies that involved converting hundreds of 2D drawings into 3D models. Why? There are a lot of important benefits surrounding 3D models that 2D drawings can’t compete with.
Useful for Rendered Images
Whenever we discuss rendered images, we talk about the construction industry. Whenever you see a sign advertising an upcoming house, business, or room, it typically comes with a 3D render as well.
The render allows you to visualize the space and get a scale for things. This same type of 3D rendering is used by engineers throughout different industries. You can use a rendering of your automotive design to put together a full photoshoot of the car before manufacturing even starts.
Rendered images can be incredibly high-quality and feature great surface and material details. In a lot of cases, it’s hard to differentiate between a render and a real picture.
Perform Static and Dynamic Tests
You can take your 3D model in CATIA, SolidWorks, Inventor, Creo (and more) and start performing engineering tests on it. A common option is to do a static test and simulate the loading condition of the bracket, for example. The simulation will show how the bracket will flex, whether it will survive the load, and what factor of safety you’re working with.
Doing the same calculation by hand could take days, and it’s easy to mess up the math. With 3D simulations, it’s much faster and comes with incredibly high confidence values.
You can also perform thermal, aerodynamic, and structural analyses.
Expedite CNC Machining
CNC machines run from G-code, and it usually requires a machinist to set up the different cuts and runs. It could take a machinist a few hours just to prepare a program for a complicated part.
With a 3D model, you can use Computer Aided Manufacturing (CAM) to create these toolpaths automatically. It might only take you a few minutes if you’re experienced enough.
Doing this will give you a G-code file that you can send directly to the machine shop and skip all of that upfront work they would otherwise have to do. This translates to faster parts and most likely a lower quote for the job.
Check Fitment with More Confidence
All 3D models are drawn in a 1-to-1 scale. That means that everything on your screen will be relative to one another if you set it up correctly. An apple on your screen will look much smaller than a car.
Since everything is scaled, you can go through a full fitment check. Ensure that holes line up, features are mating, and the interfaces of your assembly parts are perfect.
We can’t tell you how many times we found an error in a design once we tried assembling the 3D models together in Siemens NX. Even the best designer can make a simple mistake that leads to bolts missing threaded holes in other parts.
Doing the same process with 2D models is borderline impossible. With 3D models, it’s very easy if you know how to do it. How much money and time can this save you? It avoids mistakes and ensures your parts always go together.
Optimize Your Tolerance Stack
The other component of parts assembling is their independent tolerances. As you know, tolerances add up and a tolerance stack could knock your features out of position.
With 3D modeling, you can visualize where the critical dimensions are and lay out the tolerances. In certain 3D CAD programs, you can automate a lot of this process.
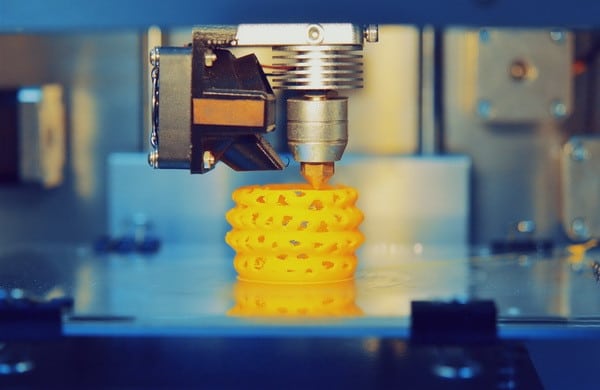
Create 3D-Printed Parts with a Click
Additive manufacturing, also called 3D printing, is becoming increasingly popular. We have a lot of clients who ask us for 3D models just so they can 3D print a part.
3D printers cannot use 2D models at all. They need an STL file which only comes from a 3D model. You might have noticed an “Additive Manufacturing” button on your 3D CAD software somewhere. If you have a 3D printer on the same network that your computer is on, you can physically start a 3D print with the click of a button.
This saves a ton of time, and it’s hard to understand the full scale until you try it for yourself.
Even if you’re going to shop out your 3D-printed parts, you’ll need a 3D model for the quote. Again, 3D printers can only use 3D models to start making parts.
Conclusion
As you just learned, converting from 2D to 3D CAD is very important. It will avoid added stress, save you time, and protect your budget. If you want to get your 2D drawings converted to 3D CAD, you can reach out to CAD/CAM Services. We work around the clock to deliver CAD Perfect solutions. Get a free quote today.
Recent Posts
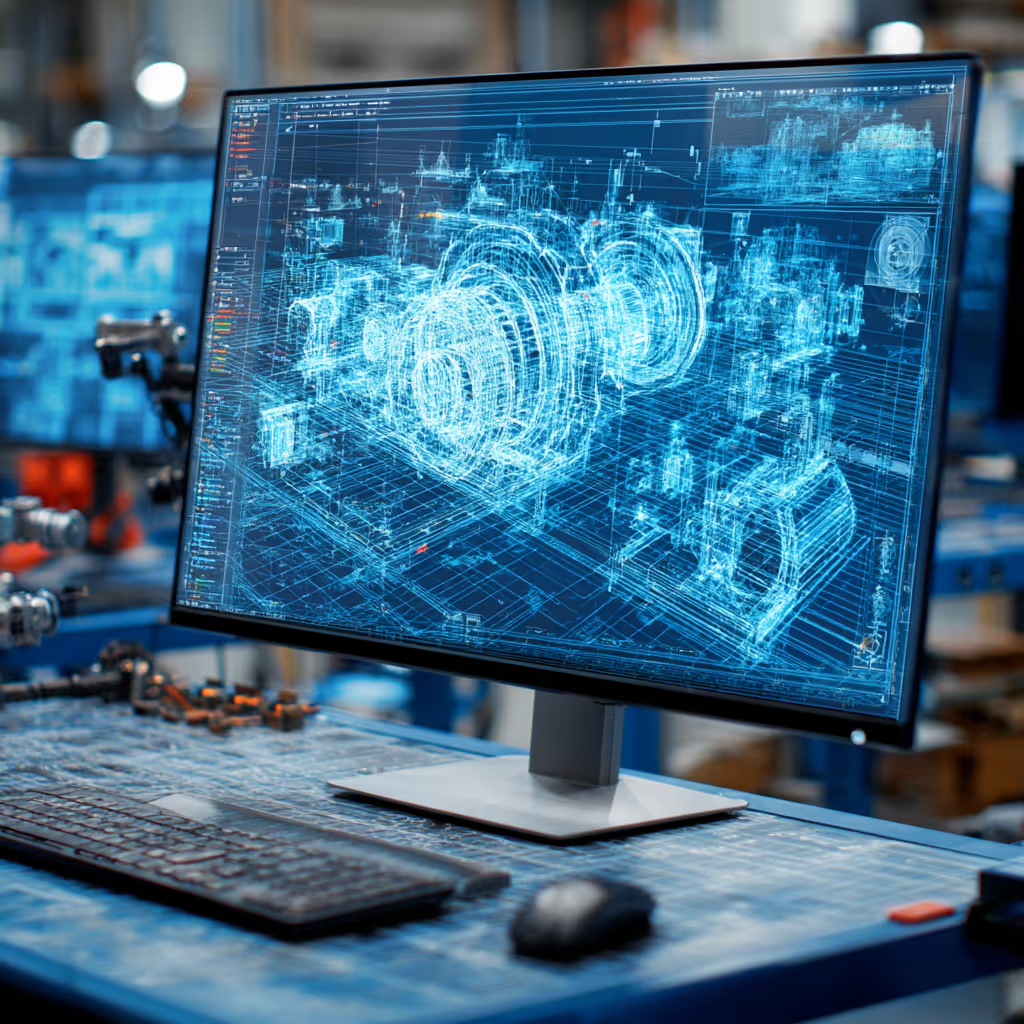
Tips for Picking the Perfect 3D CAD Viewer for Your Needs
This guide will teach you about 3D CAD viewers and outline considerations to make before picking the right one. We review 5 options and pick a clear winner.
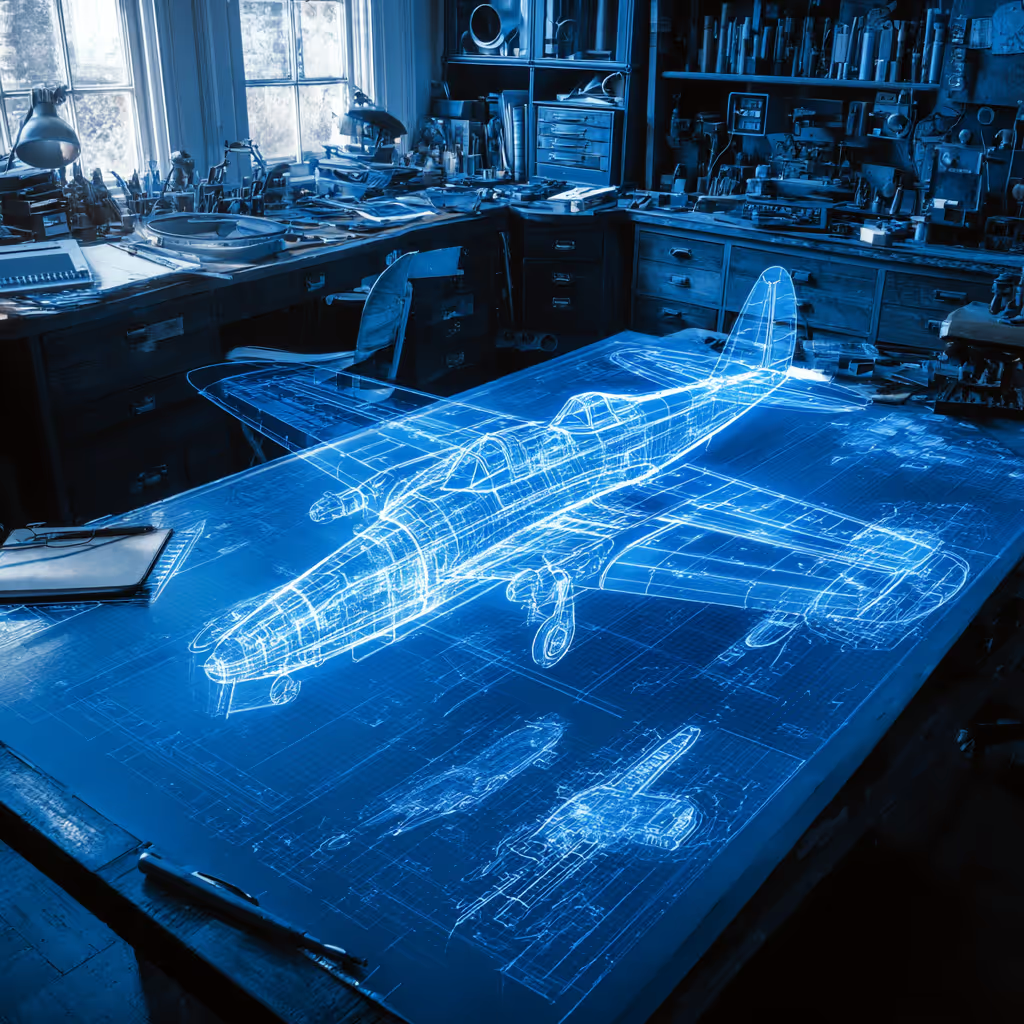
In this guide, you’ll learn how CAD/CAM Services can save you time and money during each digitization project. Digitization can make manufacturing faster than ever before.
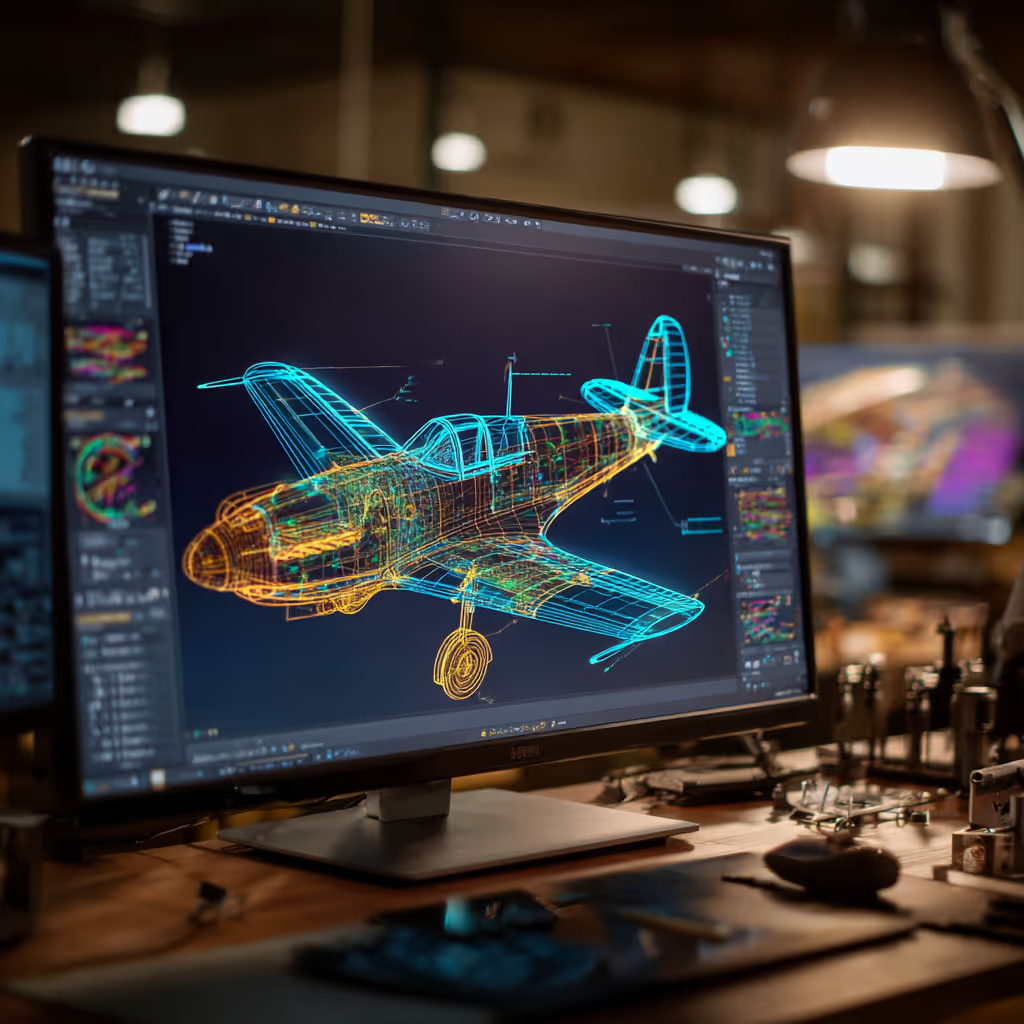
How to Build an Aircraft Model by Converting 3D-Scanned STL Files into Functional 3D STEP Files
This in-depth guide will teach engineers how to use 3D-scanned aircraft files and transform them into manufacturable 3D STEP files with fewer mistakes.