How Your Engineering Team Can Save Time and Money with 3D Printing
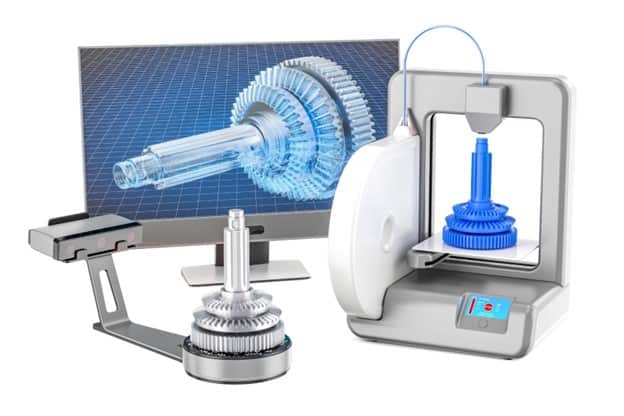
Every engineering team that we’ve talked to over the decades has had three simple goals: save time, save money, and beat the competitor. Well, 3D printing can achieve all three of these goals. Compared to traditional machining, it’s a better option in a lot of scenarios.
In this guide, we’ll explain it. We’re going to outline exactly how your engineering team can save time and money with 3D printing. We’ll give you specific examples so you understand how 3D printing can fit into your operation.
The Types of 3D Printing
3D printing comes in a lot of flavors. You can use plastic-based printers like an FDM (which you’re probably familiar with). The parts are very inexpensive, but not as strong. The machines themselves are also affordable and it’s easy to get started with them.
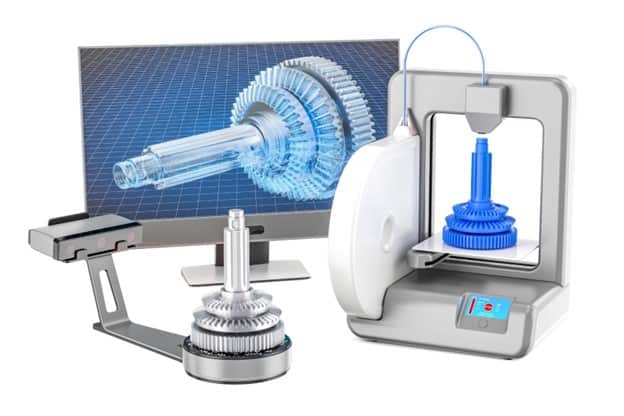
The next option is SLA, which uses resin and ultraviolet rays to make stronger parts. The machine is a little slower, more expensive, and harder to use, but the final part is much sturdier.
Another option for engineers to know about is DMLS printing. This is 3D printing that makes parts out of actual metal. It uses a laser to fuse together metal powder into a solid part, then an oven to cure it together.
With a DMLS printer, you can make parts out of titanium, stainless steel, or aluminum. The final part looks, acts, and feels just like a part you would machine on a CNC milling machine. The difference? It was 3D printed at a fraction of the cost and turnaround time.
How to Get Parts 3D Printed
To get your parts 3D printed, you can either buy and operate your own 3D printer in-house, or you can contract the work through a commercial 3D printing shop.
If you handle manufacturing or any fabrication within your company, there’s a good reason to have an in-house 3D printer. For design firms, maybe you can stick with outsourced 3D printing shops, since the need isn’t as prevalent.
3D printing is great for almost any application. We have customers in the aerospace, automotive, medical, electronics, consumer products, defense, and logistics industries (just to name a few) that have plenty of applications for 3D printing. Regardless of your industry, there’s a good chance that you can benefit from a 3D-printed part.
How Your Engineering Team Can Save Time and Money with 3D Printing
We strongly believe that no engineering team is complete without a 3D printer. The benefits are seemingly endless. These printers mesh perfectly with your 3D CAD models, so it’s easy to implement. Let’s discuss how your engineering team can save time and money by 3D printing parts.
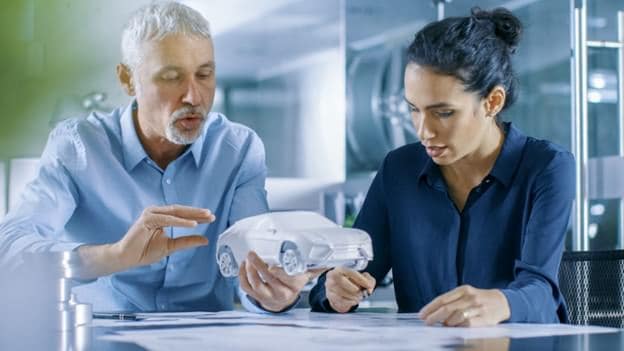
3D printing is one of the best options for prototyping a part. It’s a quick and affordable way to get parts made, re-made, and made again.
During prototyping, there are a lot of things going on. Your project probably can’t continue until you flesh out the prototype and ensure the design is perfect for the next phase.
As a result, there’s a lot of pressure when it comes to running the prototyping phase. Your budget and timeline would both be better off if you 3D print the prototype.
Instead of waiting for a machinist to take care of your part, you can have the print made within a few hours and have a new version prepared for printing tomorrow.
Quickly Go Through Iterative Designs
Another potential problem during the prototyping phase is how many iterations you need to go through. It’s commonplace to revisit your design multiple times before moving into production.
Every iteration adds even more time and money if you choose traditional machining methods to get the part made. All of these issues go away with 3D printing. Again, it’s much more affordable and the turnaround times are quicker.
It’s common to pay $20 and wait 2 days for a 3D-printed part that would otherwise cost $200 and require 2 weeks of waiting through a machine shop. This is the beauty of 3D printing as compared to machining a part.
Create Truly Customized Parts
A traditional machine shop has certain limitations when it comes to custom parts. Certain features can’t be made, and the parts can’t be too intricate. The more customized and unique the part is, the more expensive it is.
With 3D printing, the machine doesn’t care how intricate or customized the part is. The price is going to be the same, it just depends on how much material you use.
3D printing is built from 3D CAD models, and they’re pretty limitless. It means that you can put together a funky 3D model right now, and have it printed and on your desk tomorrow morning without any problems.
When there are limits to your design work, things will slow down, and the results might not be perfect for your operation. The compromises could hurt the function of the part.
By using a 3D printer to get rid of these limits, your engineering design team will enjoy more freedom, parts that work better, and more flexibility.
Fabricate at a Fraction of the Cost
We keep mentioning the price, and we want to bring it up again. The cost of 3D printing a part is significantly less expensive than machining the part.
With machining, you need to consider raw material costs (metal is expensive), labor time for the machinist to make the part, logistics issues of getting the part delivered to you, and added costs that go towards the machine shop’s profits that keep their shop running.
If you have an in-house 3D printer, you need to pay for the material used… and that’s it.
3D printing filament is incredibly affordable. Printing with plastic might cost you pennies or dollars for a full part. Doing the same print with a DMLS metal printer might bump the price up to $10 to $100, depending on how much metal powder is used.
Comparatively, the same part made in a machine shop will easily be hundreds of dollars. It’s very rare to get double-digit quotes from a machine shop.
Every single print you make on your 3D printer will save you that money. How long until the printer pays for itself?
Create Quick Parts for Destructive Testing
Destructive testing is often a part of the initial prototyping and design phase of a part. It involves doing thermal, stress, cyclic, and pressure testing until the part breaks.
If you can 3D print the parts, then you can make a batch of six parts for these tests overnight. In the morning, you can run all of the destructive tests and truly break the parts.
Doing the same operation with machined parts wastes time and money. It feels even worse, since these parts are built just to be broken. You’re better off setting a pile of money on fire.
3D printing makes it very quick and affordable to run exhaustive destructive tests.
Prepare for Mass Production or One-Off Machining
Later in your process, you might be gearing up for mass production. Alternatively, maybe you just need to make a unique one-off part to put into your product.
In either case, 3D printing will help you get to your goal. For mass production, a 3D-printed part can be used to create the mold for a urethane-cast production run. Even better, you can use a metal 3D printer to make the physical tooling with cavities that are used in an injection molding machine.
That alone can save you upwards of $100,000 each mold. Yes, injection molding tooling is incredibly expensive and typically takes 16 weeks to make, at a minimum.
You can 3D print the same tooling in metal for maybe $200 and less than a day of effort. For one-off machining, your 3D printed part can be used for testing, proof of concept, checking the fitment, getting stakeholder buy-in, or to getting funding.
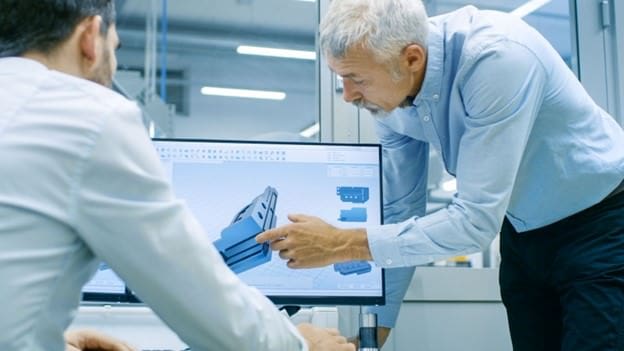
When you 3D print a part, you don’t need to make a 2D detailed drawing. A machine shop won’t be reading the dimensions and creating the part, so these drawings are useless.
Instead, the 3D printer will accept the 3D model on your CAD program. It gets converted to an STL and then into a series of G-code before running through your 3D printer.
Typically, it takes as long to make a 3D model as it does to make the 2D machining drawings. That means that each part can be done twice as fast, since the machined drawings will be skipped altogether.
Tighter Tolerances for Less Money
Whenever you design something with tight tolerances, it translates to a much more expensive quote for fabrication. Trying to make a precision part that has tolerances within 0.005” might even require a specialized shop to do the manufacturing.
With 3D printing, tight tolerances are the default. Even an entry-level machine can create parts with tolerances down to 0.005” and the operating price doesn’t change at all. Your parts are the same price. When tolerances matter, consider 3D printing.
Immediately Reverse Engineer a Part (with a 3D Scanner)
There’s a nice shortcut that you can use when it comes to reverse engineering. Instead of measuring, drafting, drawing, and modeling a part, you can do it in two steps:
3D scan it, then 3D print it. This operation takes a few minutes to complete, then the 3D-printed part will be ready in a few hours.
Compared to the days or weeks of effort doing the traditional method, this is a no-brainer.
You just saved a week of engineering time that you can place somewhere else. You also saved all the money you would have otherwise spent on labor costs to do all that.
Prove Your Concept
Whenever a new product is introduced, it has to go through a proof of concept phase. This involves making the part and making sure it actually works.
The more novel the solution, the more proving you need to do. With 3D printing, you can quickly prove out your concept and continue through the product lifecycle.
As you’ve probably noticed by now, 3D printing saves time in almost every phase of design and production.
Check for Fit
A fitment check is another very important test before going to production. In this case, you’re going to put your part into the process line, on the assembly, or in the machine to see if it fits correctly.
Even though something fits nicely on your screen in the 3D model, it might not fit in real life. This is why fitment checks are essential before getting too far.
A 3D-printed plastic part is really great at fitment checks. Even if the final part will be metal, you can check the dimensional clearances and tolerance requirements with a plastic part.
The best part? The plastic 3D-printed part will be a fraction of the cost and be done in a few hours.
You can realistically design, 3D print, and check the fit of a part all within the same working day. It doesn’t get much better than that.
This streamlines your project while saving you money.
Conclusion
As you just saw, 3D printers can save your engineering team a ton of time and money. During almost any phase of your project, a 3D printer can be used to help. All you need is a great 3D model to get started. Need help making these models and expediting your project?
That’s where our team at CAD/CAM Services can help. We’ve been in business for decades, and we’ve put together countless 3D models that were then 3D printed. We will make things easy for you and save you time. Reach out today for a free quote.
Recent Posts
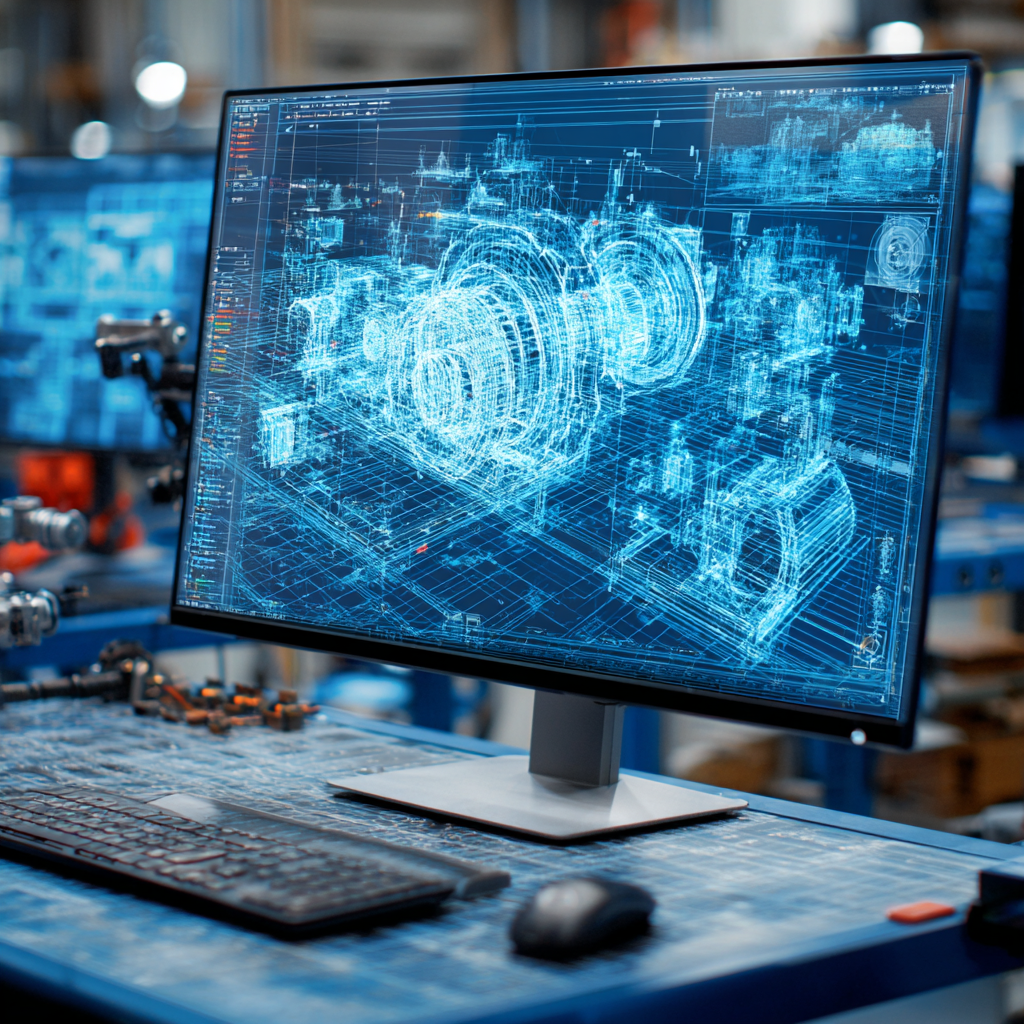
Tips for Picking the Perfect 3D CAD Viewer for Your Needs
This guide will teach you about 3D CAD viewers and outline considerations to make before picking the right one. We review 5 options and pick a clear winner.
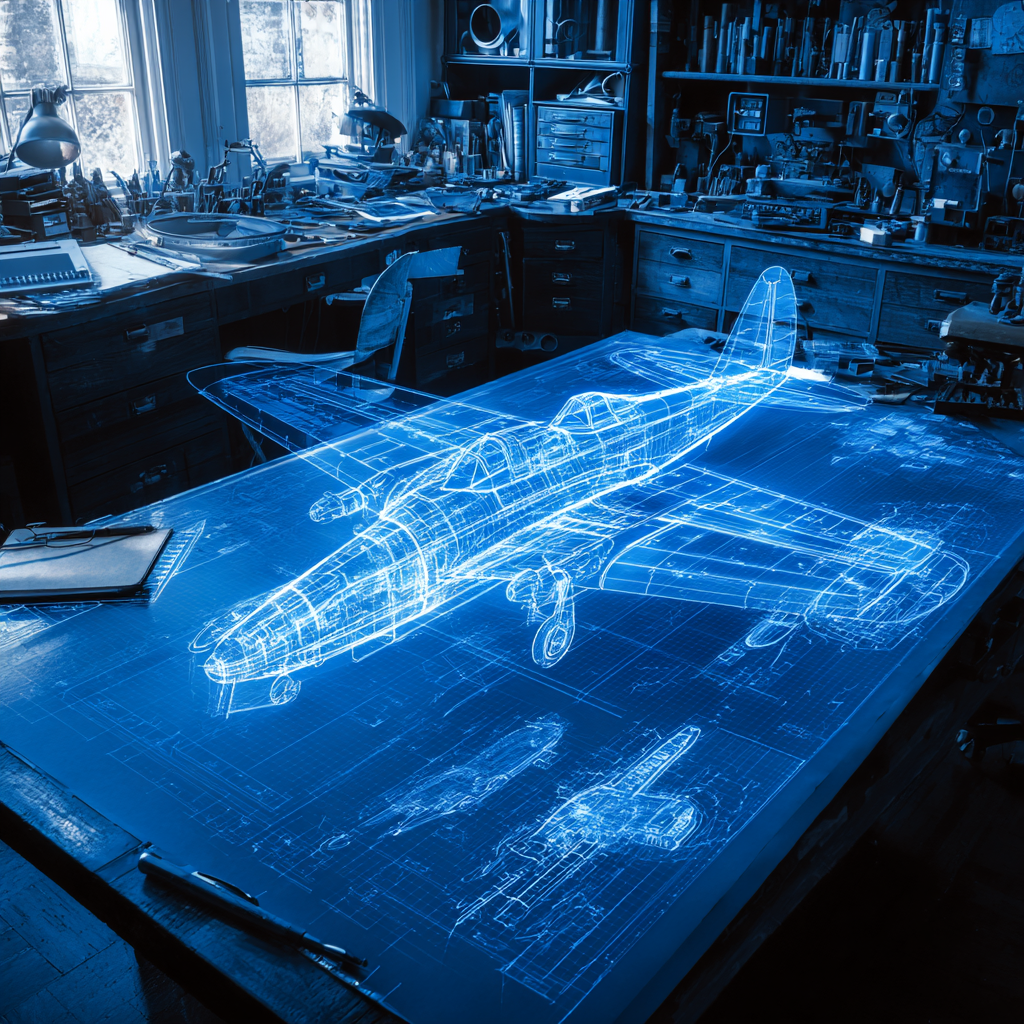
In this guide, you’ll learn how CAD/CAM Services can save you time and money during each digitization project. Digitization can make manufacturing faster than ever before.
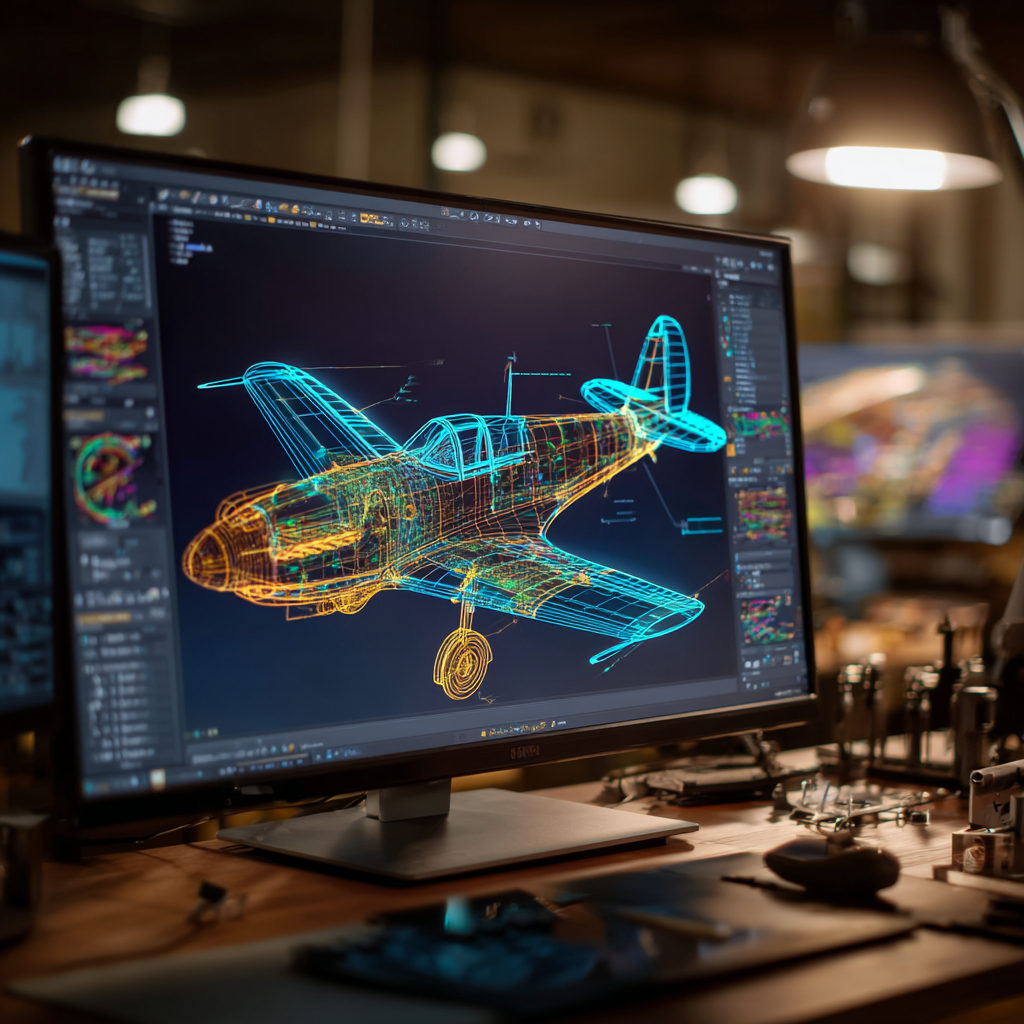
How to Build an Aircraft Model by Converting 3D-Scanned STL Files into Functional 3D STEP Files
This in-depth guide will teach engineers how to use 3D-scanned aircraft files and transform them into manufacturable 3D STEP files with fewer mistakes.