Blogs
Discover the latest CAD, 3D modeling, scanning, and more updates. Dive into our articles and stay informed to enhance your expertise in the field.
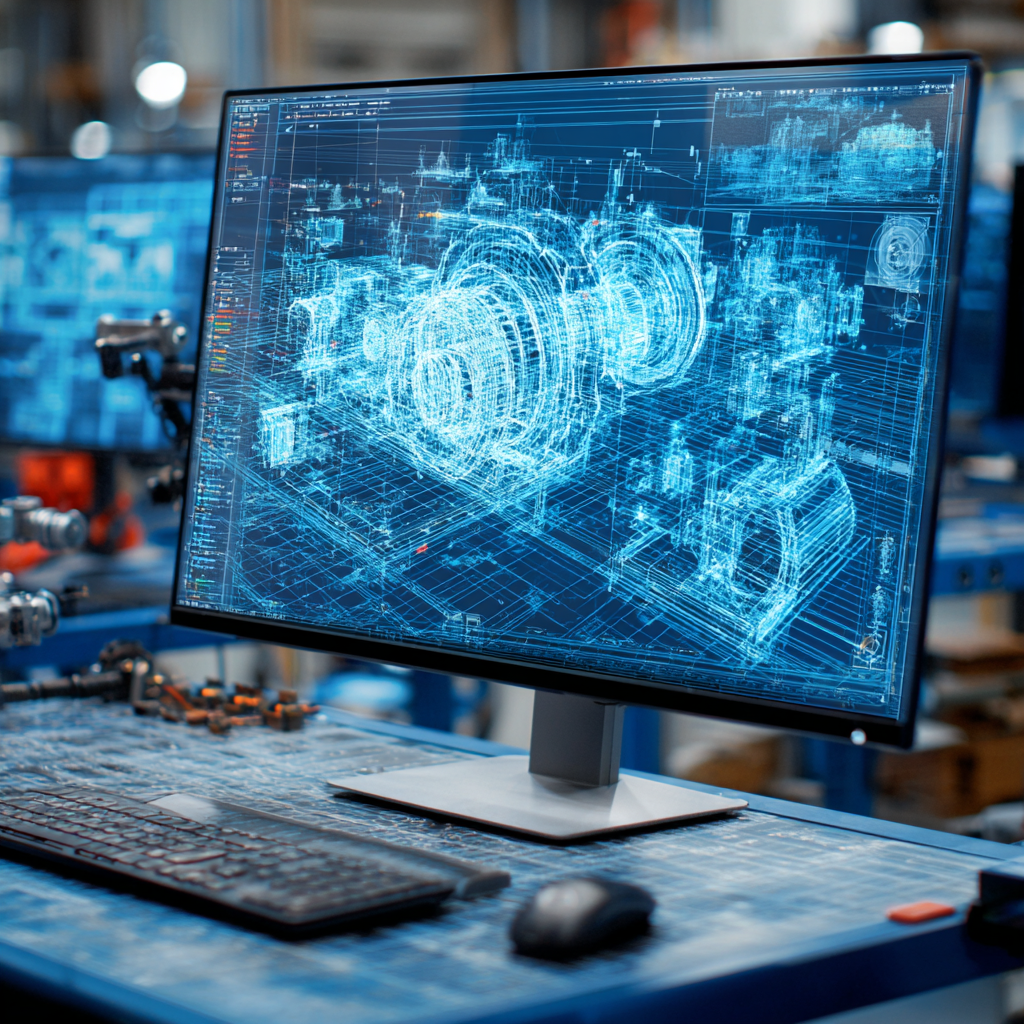
This guide will teach you about 3D CAD viewers and outline considerations to make before picking the right one. We review 5 options and pick a clear winner.
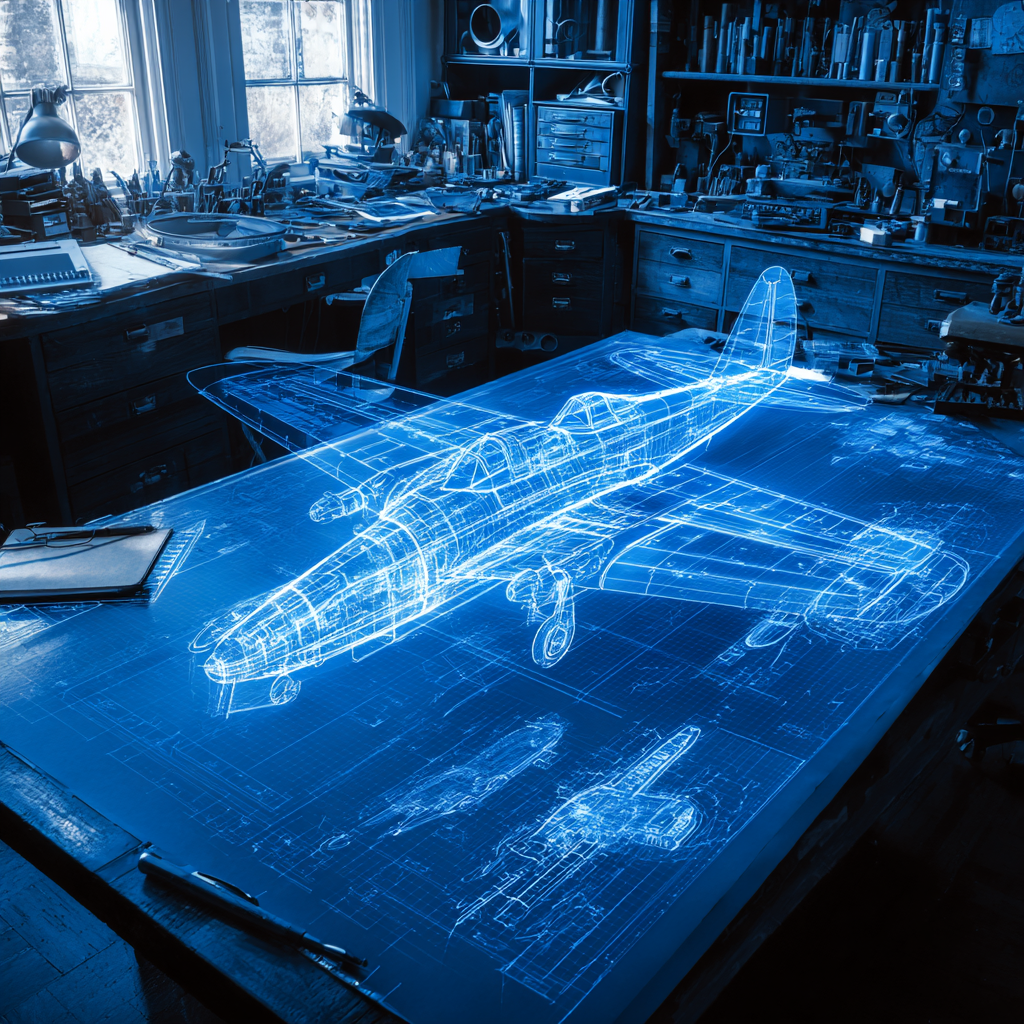
In this guide, you’ll learn how CAD/CAM Services can save you time and money during each digitization project. Digitization can make manufacturing faster than ever before.
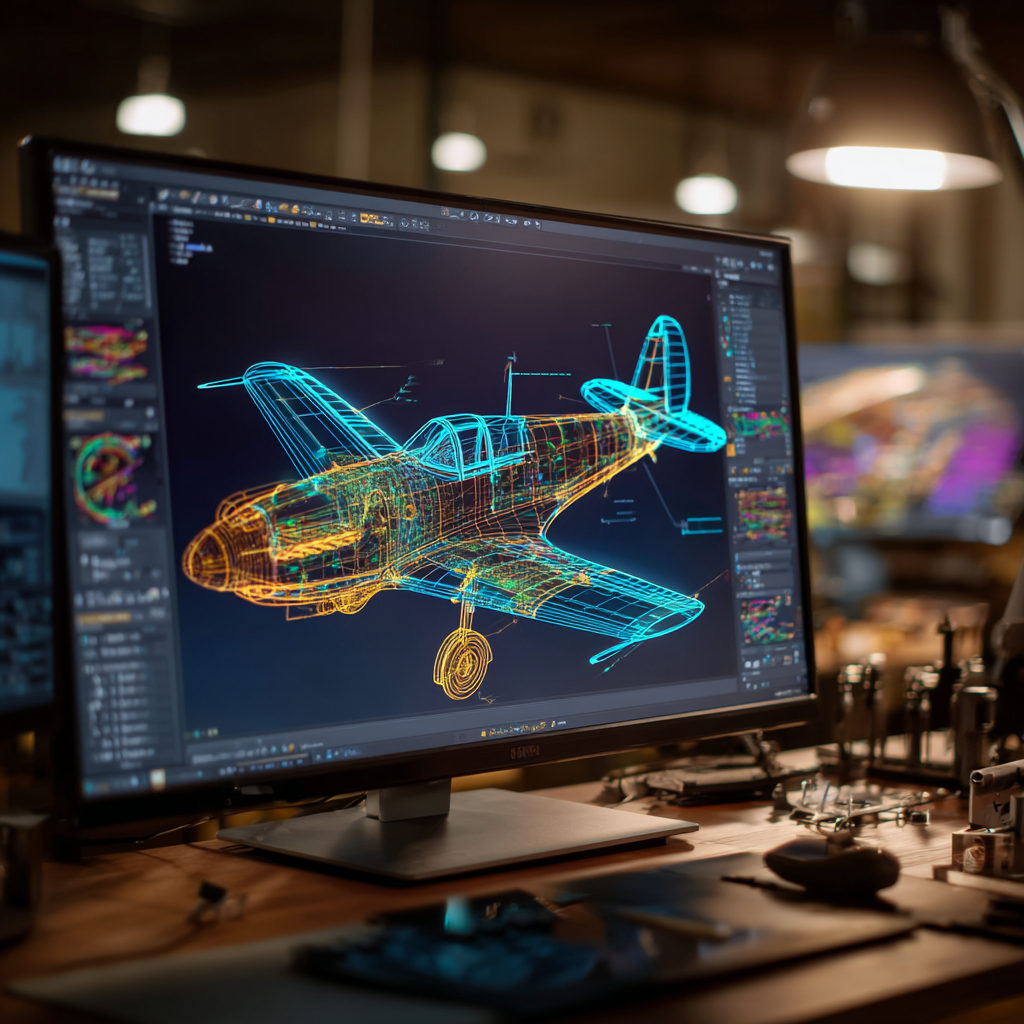
This in-depth guide will teach engineers how to use 3D-scanned aircraft files and transform them into manufacturable 3D STEP files with fewer mistakes.
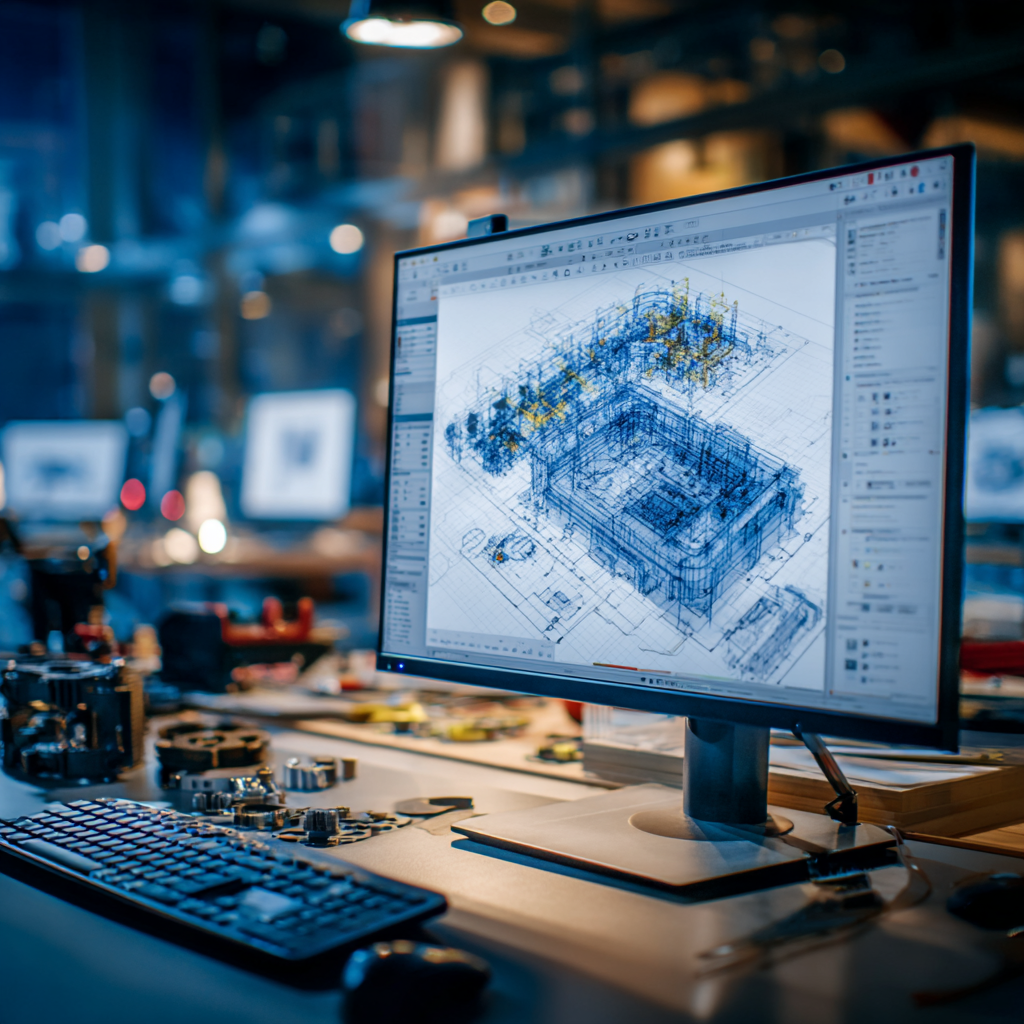
This beginner’s guide will walk you through the problem with “extra large” CAD models, how it impacts your work, and some common ways to avoid them.
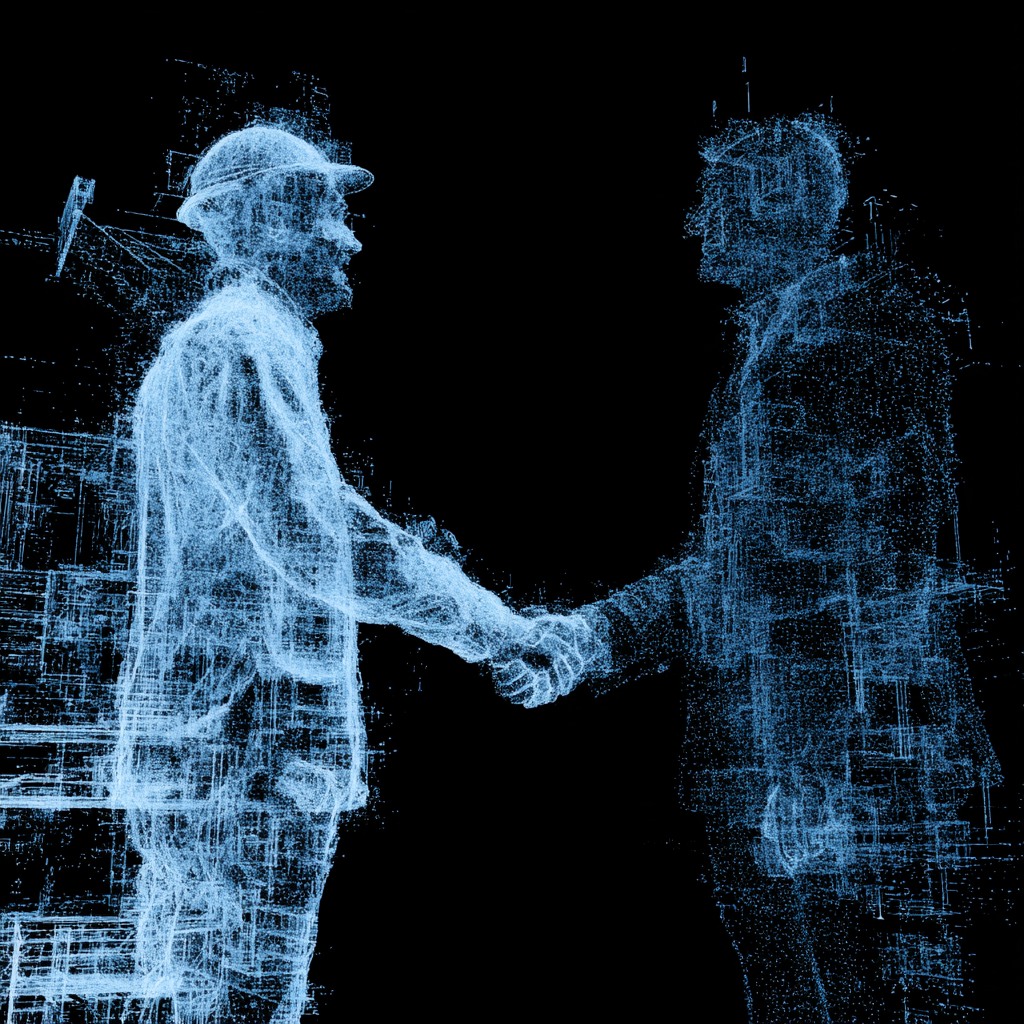
This guide gives an in-depth look at the pros and cons associated with outsourcing engineering services, whether it’s a portion of the project or the whole thing.