All About 3D Scanning: What it Is, How it Works
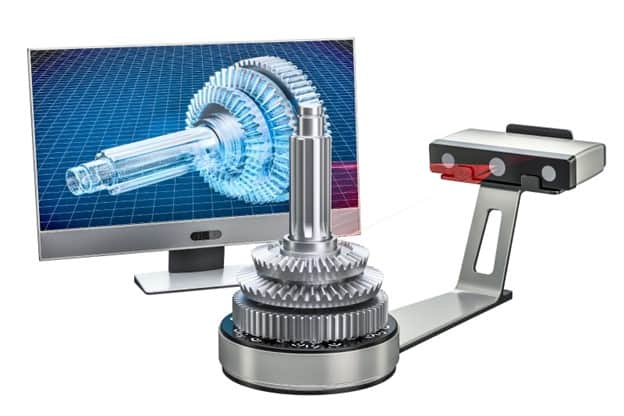
As you’re looking for quicker and more accurate ways to measure your parts, you might have stumbled across 3D scanning. This technology isn’t necessarily new, but new developments are making this technology more useful than ever.
In this guide, we’ll talk all about 3D scanning. We’ll cover what it is, how it works, and when you might use it.
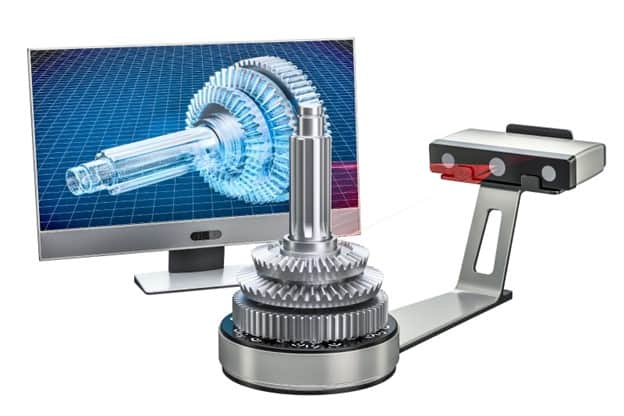
What Is 3D Scanning?
3D scanning is a non-contact way to measure a part and create a digital copy of the part. 3D scanners will use either light or laser beams to shine across the surface of your part, collect points of data, then map out a digital version of the part it just scanned.
A lot of modern engineering companies use 3D scanning to quickly reverse engineer an object that they have. A wide range of objects can be 3D scanned, and there’s no real limit to the size or accuracy. As new 3D scanners come out each year, they become even more versatile.
How 3D Scanning Works
3D scanning works by finding a bunch of points in space. These points are the surface of the object being scanned. A separate piece of software will compile all of these points and make a solid CAD model from the scan.
The scanner will shoot out beams of light or lasers, then cameras or sensors will measure how far away the beams are. The beams will map the surface of the scanned part, and the beams move around until the full part is scanned.
When You Might Use a 3D Scanner
Now that you know how they work, let’s discuss when you might use a 3D scanner. There are a number of industries that benefit from this technology, but we’ll focus on engineering.
Reverse Engineering
Reverse engineering is probably the most common reason to use a 3D scanner. When you need to measure a part and make manufacturing drawings, your options are to either get the original drawing from the vendor, measure it with calipers and a tape measure, or 3D scan the object.
If you can’t track down the original drawing or you don’t know where the part came from, then 3D scanning is your only option. You would simply rotate the part while 3D scanning it, then get a full CAD model of the object.
Confidence in Fitment
Let’s say you have an assembly that you need to fit a new part into. With 3D scanning, this process becomes a lot simpler.
Tolerance studies and precise measurements can only get you so far. A 3D scan will show you the as-built version of the assembly, so all of the added noise will be taken out and there won’t be any assumptions.
You’re left with the truest version of your assembly. You can take the scanned model and start playing around on Siemens NX or SolidWorks to put your new part in the assembly. From there, you’ll know exactly if the part fits.
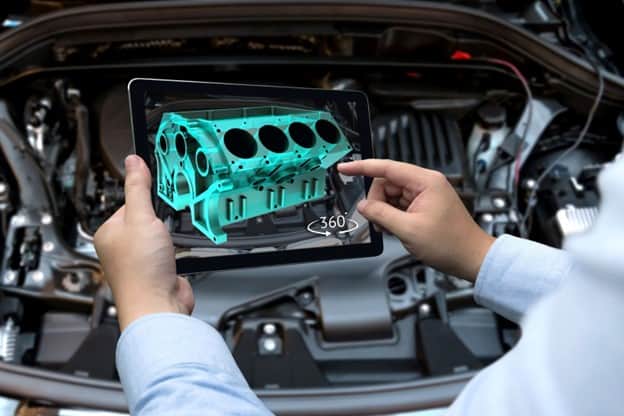
Non Contact Measuring
Another benefit of 3D scanning is that it doesn’t have to come in contact with the object like a CMM or calipers do. This is a big reason why historians started 3D scanning old sculptures and busts like The Thinker and the David of Michelangelo. Touching these statues could damage them, but scanning them was a safe alternative.
This same benefit can apply to any system in your facility. Maybe you’re dealing with objects that have toxic chemicals on them, or sensitive parts that deteriorate if they’re touched. Since 3D scanning doesn’t come in contact with the part it scans, you don’t have to worry.
Quickly Measuring Huge Parts
What are you supposed to do if you want to measure your warehouse? You could send out an intern with a tape measurer, but there’s no saying how accurate the final model will be. In fact, there’s no reliable way to map out a full building in 3D with physical measuring devices.
This is where you might turn to a 3D scanner. You can use a scanner to get a full CAD model of your warehouse within a few minutes. It’s really impressive to see these scanners map out a huge building.
You’re left with a dimensionally accurate version of your warehouse. You don’t have to guess whether or not the new piece of equipment will fit — instead, put the 3D model of the equipment into the 3D model of your warehouse.
When Detail Is Important
If you need to get precise dimensions of a part, you can either use a CMM or 3D scanner. Using a CMM takes a ton of time and it’s very costly. At the end, there are still limitations when it comes to dimensional accuracy. Most CMM machines can’t measure tiny details and cracks, but 3D scanners can.
Since the 3D scan goes right into a CAD model, you don’t even have to convert the measurements. You’re left with a model that’s ready to get to work. If you need to know the exact profile of a propeller, then 3D scanning is a great choice.
Types of 3D Scanning
Now, let’s talk about the different types of 3D scanning. Not all scanners work the same way. To get the best results, you need to start with the right scanner.
DIY 3D Scanning
There’s a way to use your cell phone as a DIY 3D scanner. You have to download an app and probably buy a small turntable to get better results, but that’s it.
While this is fun for hobbyists, it doesn’t work for engineers like us. It lacks the detail, precision, and function that you’re looking for.
Structured Metrology-Grade 3D Scanners
There is a series of metrology-grade 3D scanners that use structured light. These work with either blue or white light that gets projected onto the object.
Sensors on the scanner will then measure how far away each pixel of light is. From there, it can make a map of the part in 3D.
Laser Scanners
Stepping away from light, you’ll find a collection of different laser 3D scanners. These scanners come in a range of prices, sizes, and functions.
At its core, a laser scanner work by shining a laser on the object you’re trying to measure. A series of cameras will then record how the laser travels across the object, compiling a series of dots.
These dots come together to make a point cloud (a cloud of points), which is then converted to a solid model on your favorite CAD software.
Conclusion
You just learned a ton about 3D scanning. We covered what it is, how it works, and when you might use it. If you’re interested to learn more or you want to get something 3D scanned today, reach out to our team at CAD/CAM Services.
We are a full-service engineering team. Our goal is to deliver exceptional results and help with your engineering projects. We have full 3D scanning capabilities and additional modeling services that will expedite your project. Reach out for a free quote today.
Recent Posts
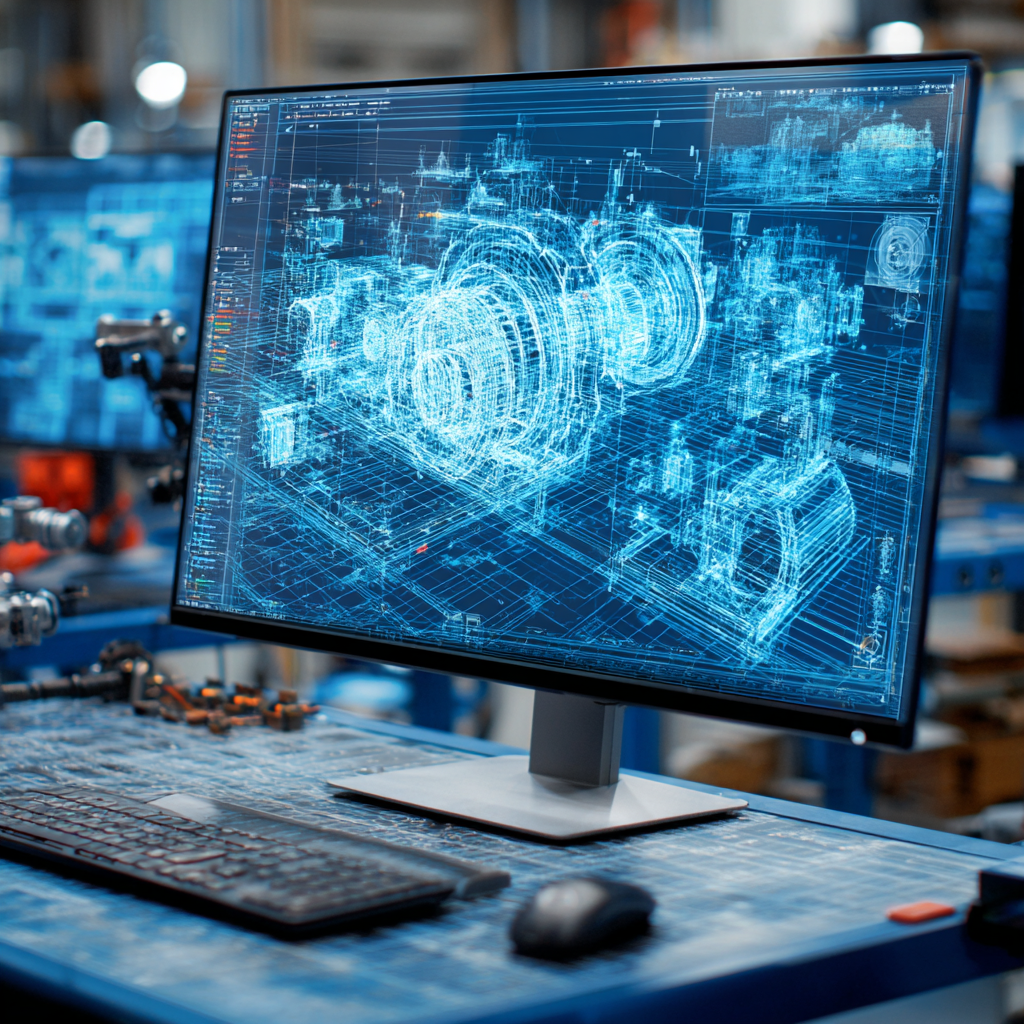
Tips for Picking the Perfect 3D CAD Viewer for Your Needs
This guide will teach you about 3D CAD viewers and outline considerations to make before picking the right one. We review 5 options and pick a clear winner.
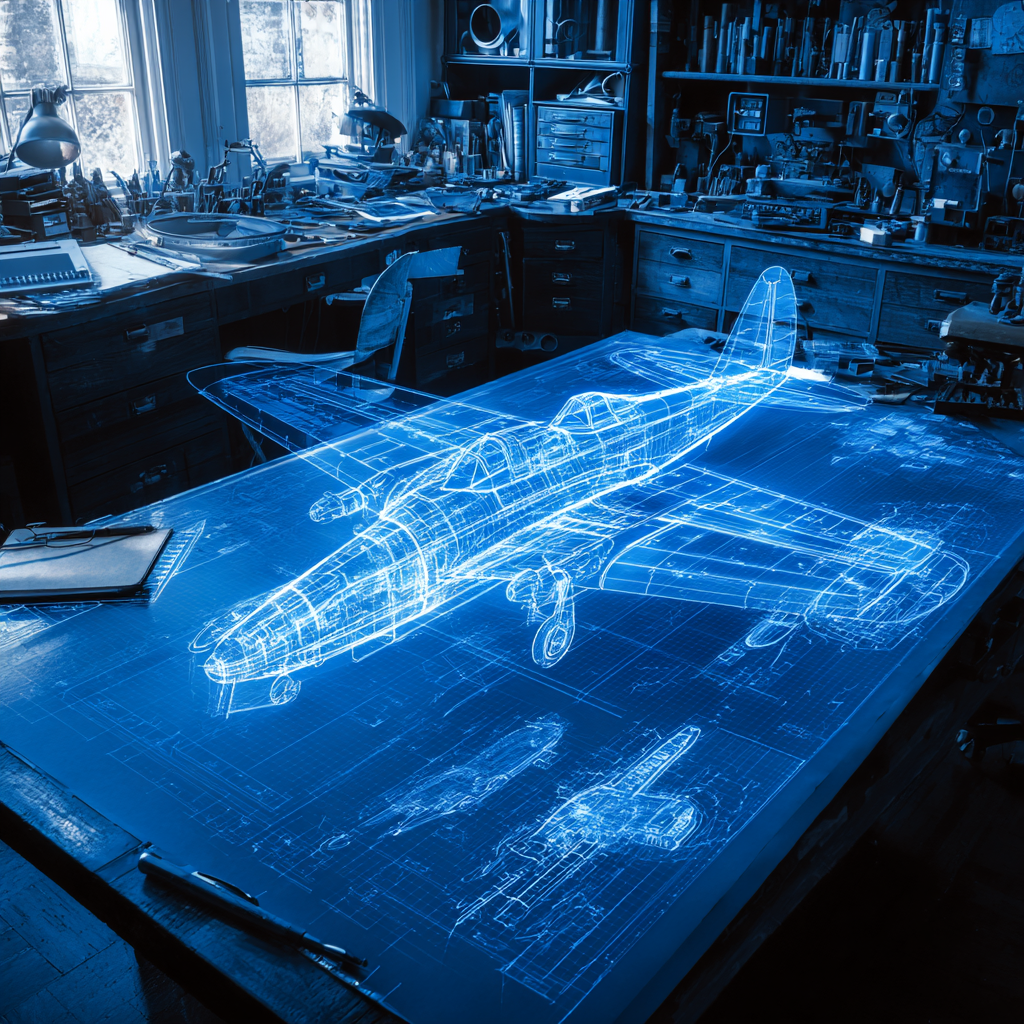
In this guide, you’ll learn how CAD/CAM Services can save you time and money during each digitization project. Digitization can make manufacturing faster than ever before.
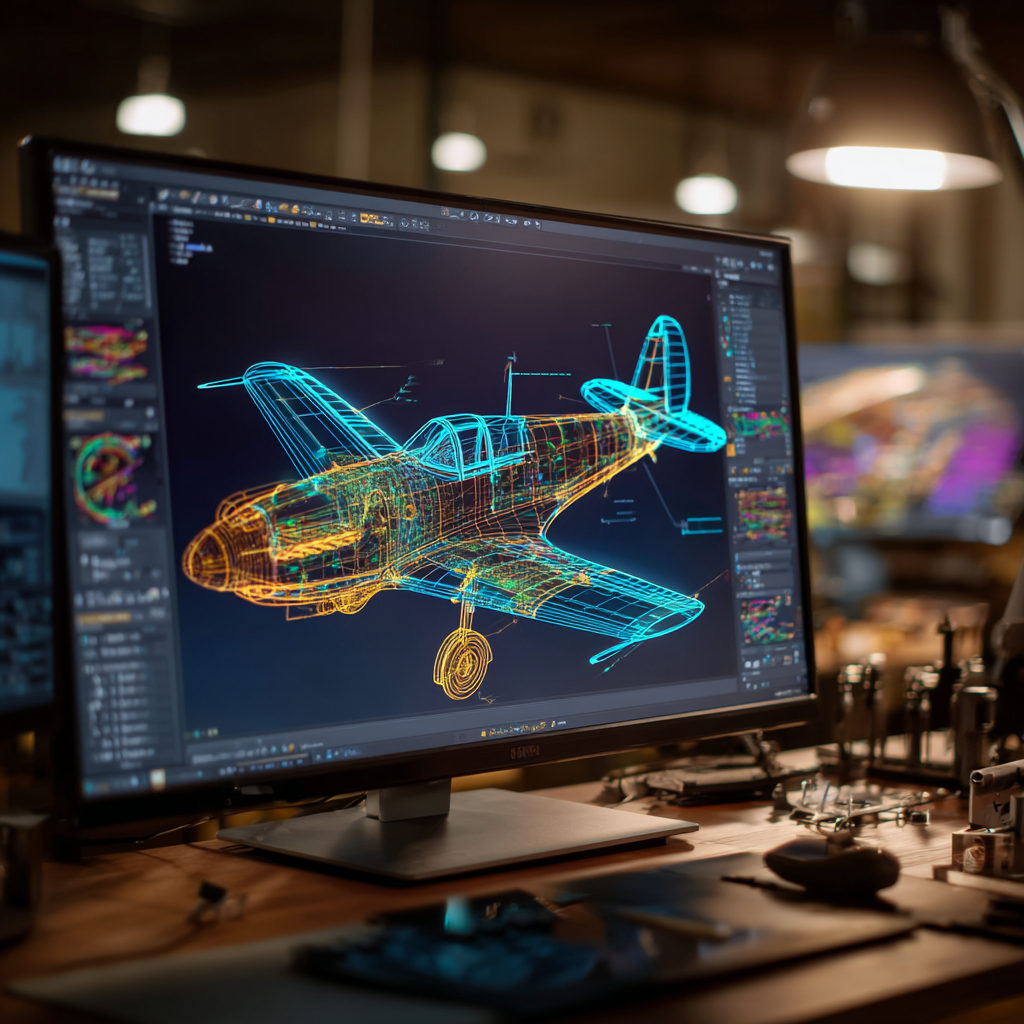
How to Build an Aircraft Model by Converting 3D-Scanned STL Files into Functional 3D STEP Files
This in-depth guide will teach engineers how to use 3D-scanned aircraft files and transform them into manufacturable 3D STEP files with fewer mistakes.