3D Scanning & Data Capture Considerations and Processes
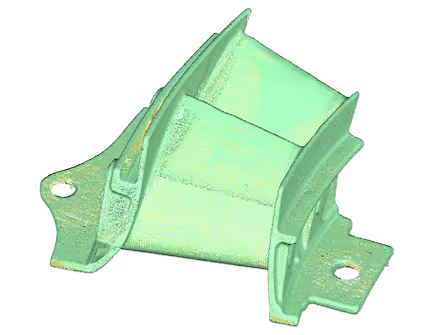
3D Scanning & Data Capture Considerations and Processes
3D Scanning is a method of digitally capturing the shape of a physical object without touching or affecting the object in any way. It is totally non-destructive. Laser scanning is the fastest, most accurate, and automated way to acquire 3D digital data. This technology digitally captures the shape of physical objects using a line of laser light.
3D scanning is used for the measurement and inspection of contoured surfaces and complex geometries which require massive amounts of data for their accurate description and where doing this is impractical with the use of traditional measurement methods or a touch probe.
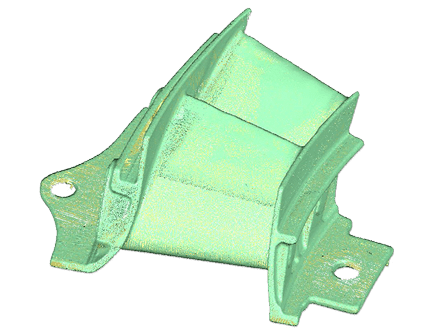
3D scanners create “point clouds” of data from the surface of an object. By using specialized software, the point cloud data is used to create a 3D CAD model of the part’s geometry. In other words, 3D scanning is a way to capture a physical object’s exact size and shape into a computer as a digital 3-dimensional representation. 3D scanners measure fine details and capture free-form shapes to quickly generate highly accurate point clouds.
The CAD model that is developed from the point cloud data enables the precise reproduction of the scanned object, or the object can be modified in the CAD model to correct imperfections. Thus, 3D scanning is ideally suited to scanning is ideally suited to activities such as reverse engineering and scan-to-cad comparisons.
Considerations
- What are the dimensions your part(s)? Are you able to handle them yourself, or do you need help?
- How complex are your part(s)? Are there internal features to be scanned?
- How do you intend to use the resulting scan data? Reverse Engineering? 3D Printing? Comparing Scan to CAD?
- What are your requirements for dimensional call outs? Are you looking for first article inspection?
Processes
An object that is to be laser scanned is placed on the bed of the digitizer. Specialized software drives the laser probe above the surface of the object. The laser probe projects a line of laser light onto the surface while 2 sensor cameras continuously record the changing distance and shape of the laser line in three dimensions (XYZ) as it sweeps along the object.
- Resulting Data —The shape of the object appears as millions of points called a “point cloud” on the computer monitor as the laser moves around capturing the entire surface shape of the object. The process is very fast, gathering up to 750,000 points per second and very precise (to ±.0005″).
- Modeling Choice Depends on Application — After the huge point cloud data files are created, they are registered and merged into one three-dimensional representation of the object and post-processed with various software packages suitable for a specific application.
- Point Cloud Data for Inspection —If the data is to be used for inspection, the scanned object can be compared to the designer’s CAD nominal data. The result of this comparison process is delivered in the form of a “color map deviation report,” in PDF format, which pictorially describes the differences between the scan data and the CAD data.
Recent Posts
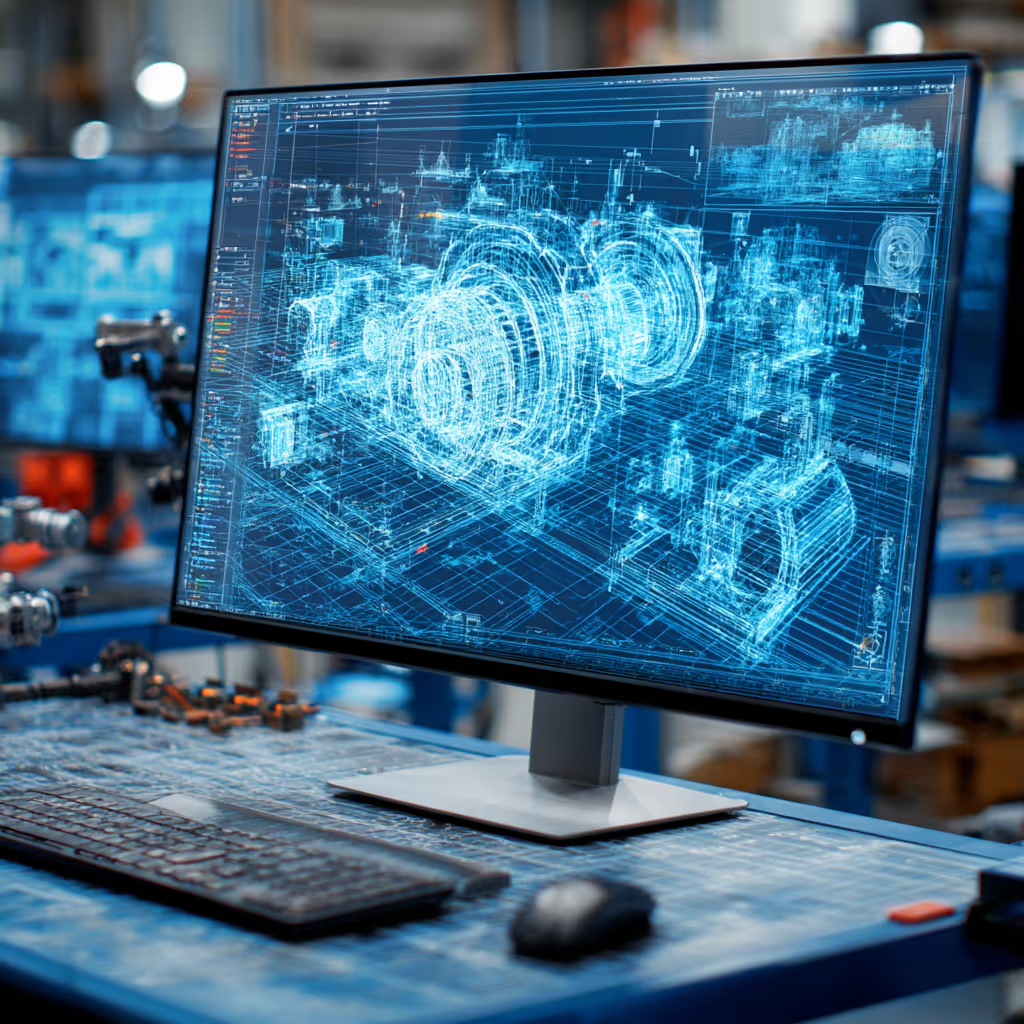
Tips for Picking the Perfect 3D CAD Viewer for Your Needs
This guide will teach you about 3D CAD viewers and outline considerations to make before picking the right one. We review 5 options and pick a clear winner.
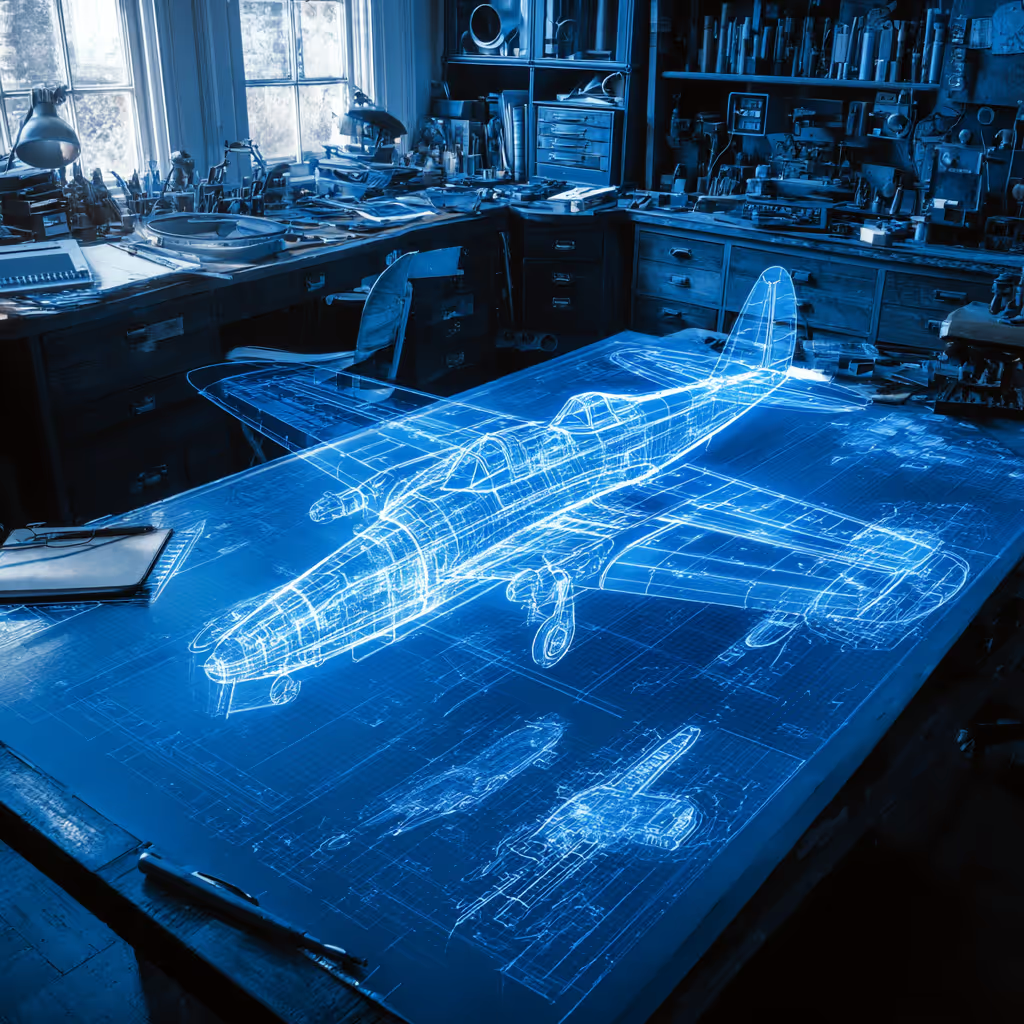
In this guide, you’ll learn how CAD/CAM Services can save you time and money during each digitization project. Digitization can make manufacturing faster than ever before.
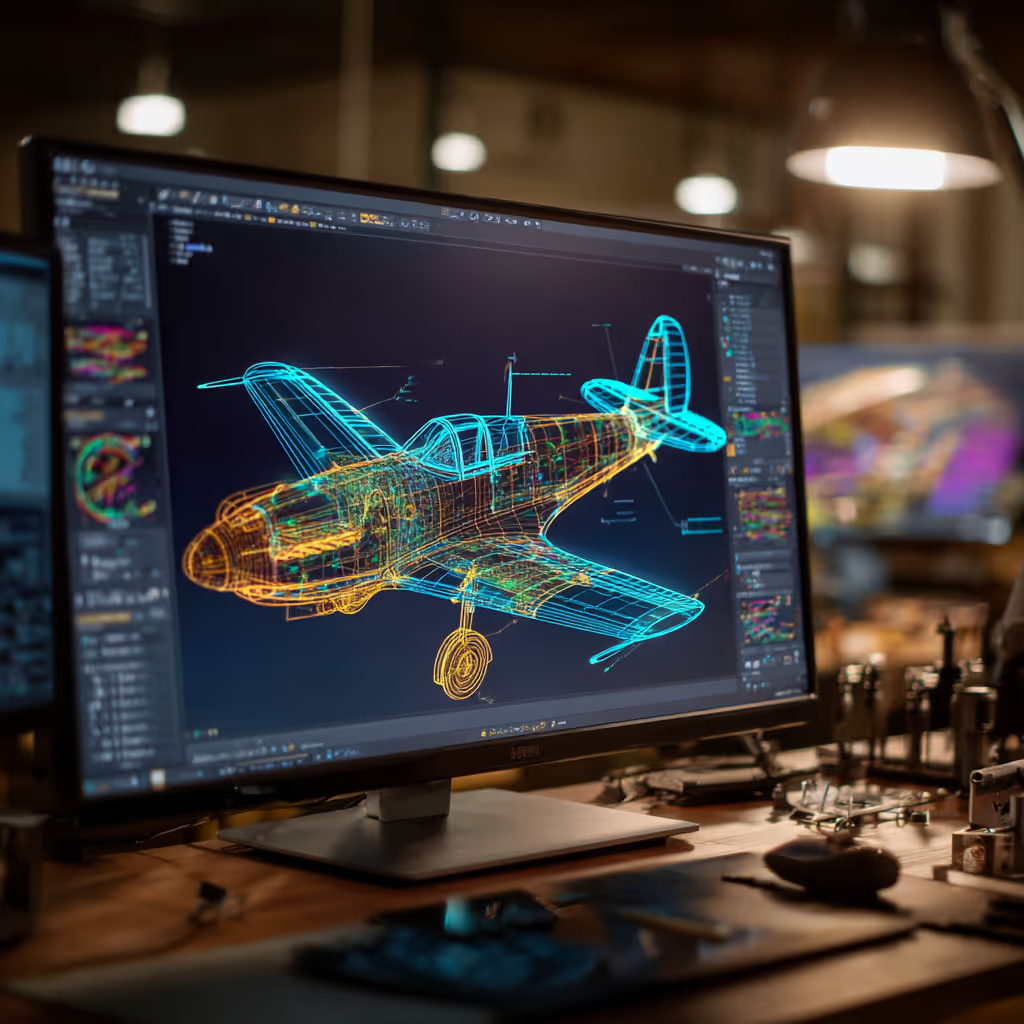
How to Build an Aircraft Model by Converting 3D-Scanned STL Files into Functional 3D STEP Files
This in-depth guide will teach engineers how to use 3D-scanned aircraft files and transform them into manufacturable 3D STEP files with fewer mistakes.