PDM: Managing Product Data
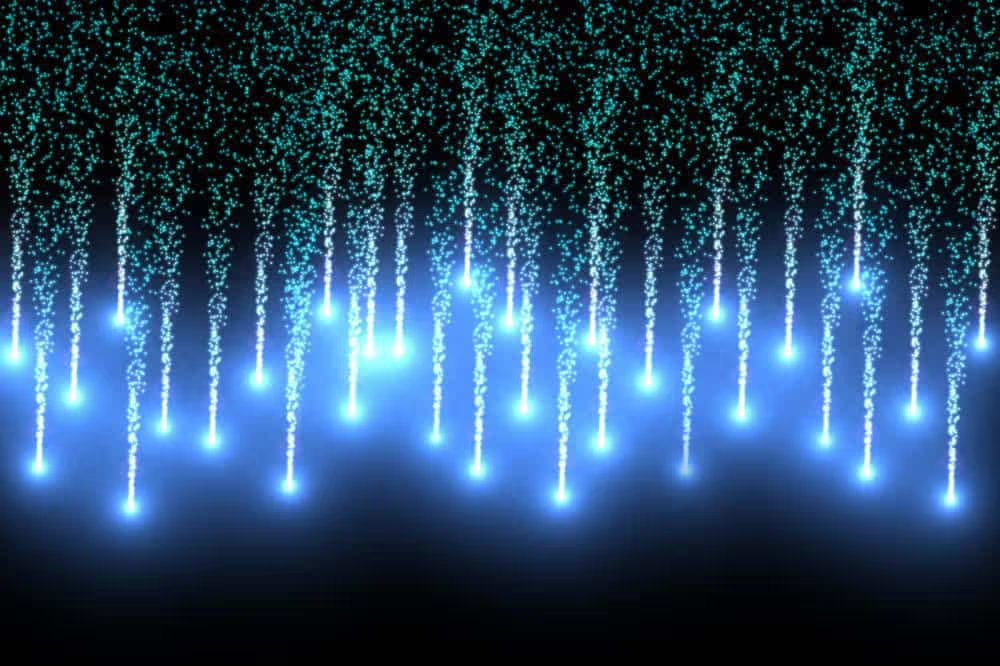
PDM: Managing Product Data
If you’re part of a design team, you know how important Product Data Management (PDM) can be. There are seven reasons why PDM is so important:
- Better Control – Engineering data is time-consuming to compile and can be unwieldy to manage (interrelationships, large data sets, etc.). PDM helps design teams and engineers communicate and stay on the same page.
- Increased Productivity – If you don’t want to miss your production deadline, then you need to be able to find the right information fast.
- Error Elimination – Cost control requires reducing manufacturing waste by ensuring that you always work on the latest revision.
- Enterprise Connectivity – Sharing information with other business systems (ERP/MRP).
- Collaboration – Communicating information to suppliers/customers.
- Certification – Assisting with standardizing processes (FDA/ISO/FAA/TQM).
- Compliance – Helping ensure data security (ITAR, etc.).

PDM software systems manage and synchronize your design data across your entire enterprise with a single, easily deployable solution that integrates with your CAD applications. Such a secure storage vault lets you share access to your 3D design environment and associated files so that all participants — engineering through manufacturing –“ know what’s going on. Information sharing and collaboration makes designs more robust, while security features automatically protect your intellectual property with automated version and revision control systems.
How Many Design Teams Use PDM?
According to a recent survey conducted by Engineering.com, almost half of all product design teams do not have a formal PDM system. Generally, smaller design teams are less likely to have a formal PDM, while large teams such as those in the Defense and Aerospace Industries are highly likely to have a formal PDM.
What do Do Design Teams like About PDM?
Design teams like easy connectivity to their CAD systems and they like the easy way that PDM allows them to collaborate with CAD CAM Services, may customize their workflows to include our team.
How and Where Does PLM Relate to PDM?
While the PDM system serves as a product and process knowledge repository, promoting secure data exchange and integration among design engineers, project managers, sales managers, users, QC managers and external CAD service providers, a PLM is a business strategy which deals with managing the entire lifecycle of a product by integrating multiple software tools, database, and management techniques.
Generally, CAD service providers don’t get involved in the PLM side of the process, unless part of the product lifecycle involves reverse engineering and retrofitting of parts. In that case, we are often called upon to update the drawings, models, and data in the PDM system.
Recent Posts
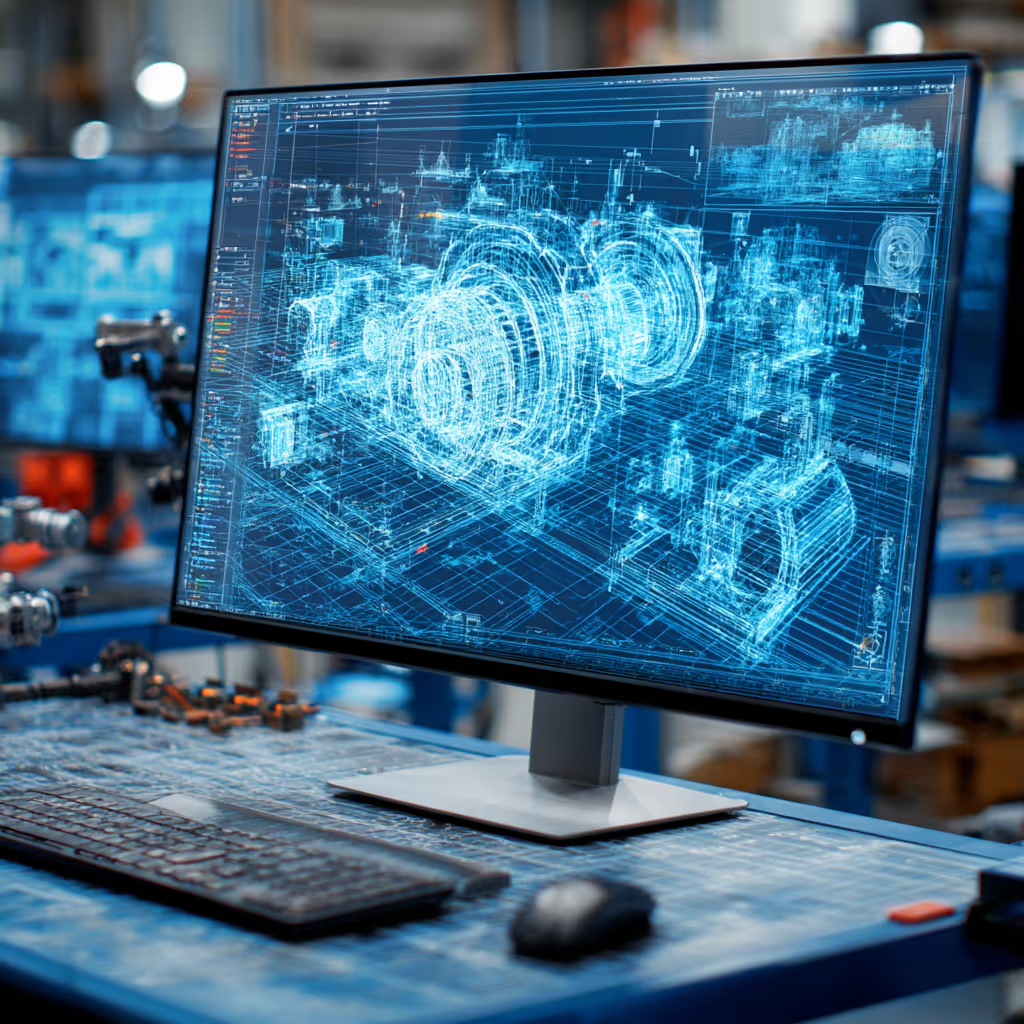
Tips for Picking the Perfect 3D CAD Viewer for Your Needs
This guide will teach you about 3D CAD viewers and outline considerations to make before picking the right one. We review 5 options and pick a clear winner.
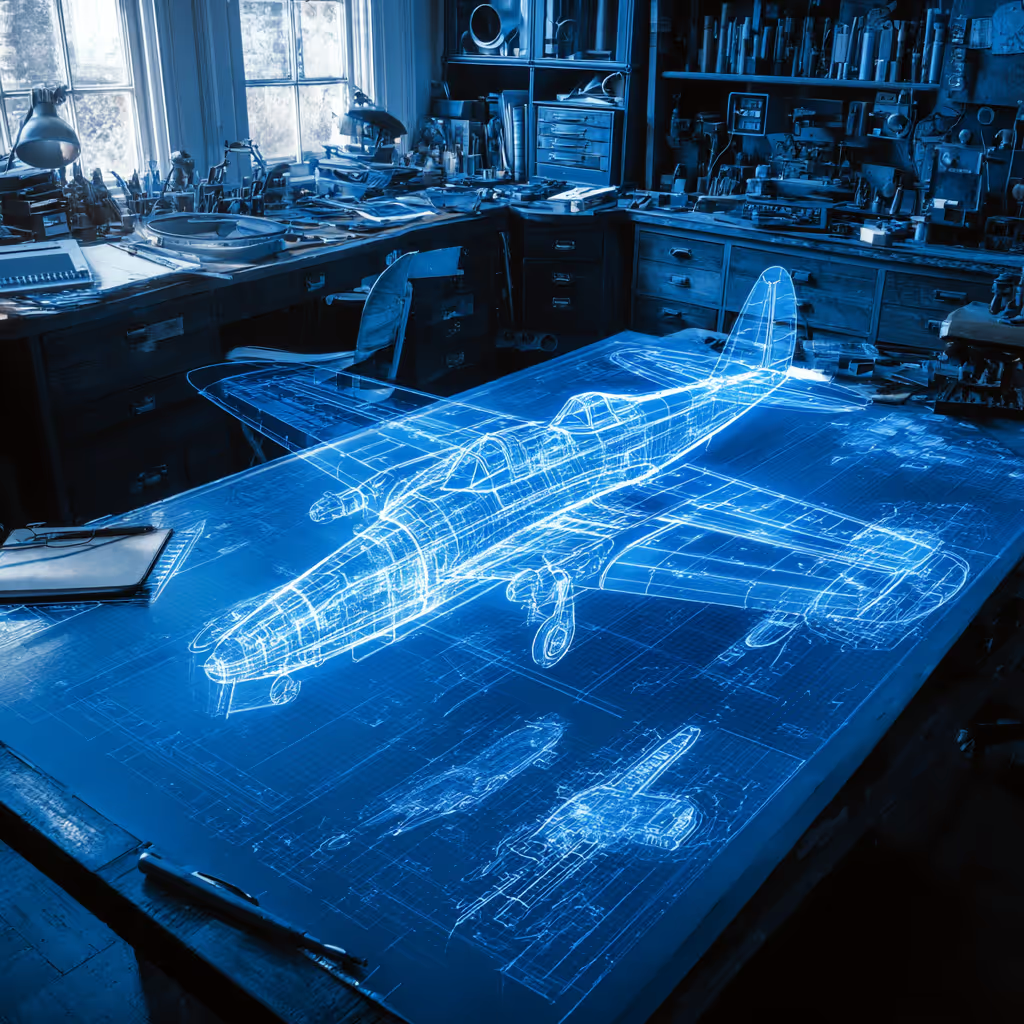
In this guide, you’ll learn how CAD/CAM Services can save you time and money during each digitization project. Digitization can make manufacturing faster than ever before.
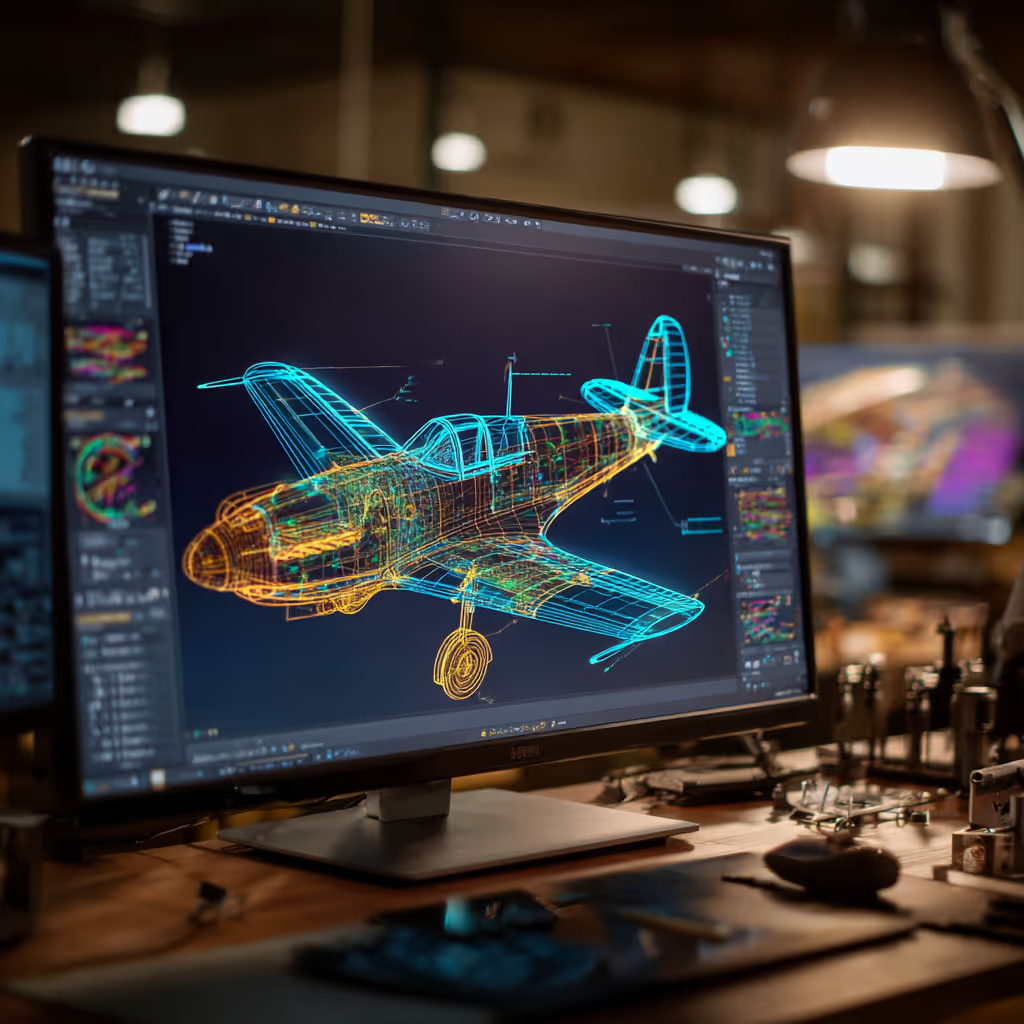
How to Build an Aircraft Model by Converting 3D-Scanned STL Files into Functional 3D STEP Files
This in-depth guide will teach engineers how to use 3D-scanned aircraft files and transform them into manufacturable 3D STEP files with fewer mistakes.